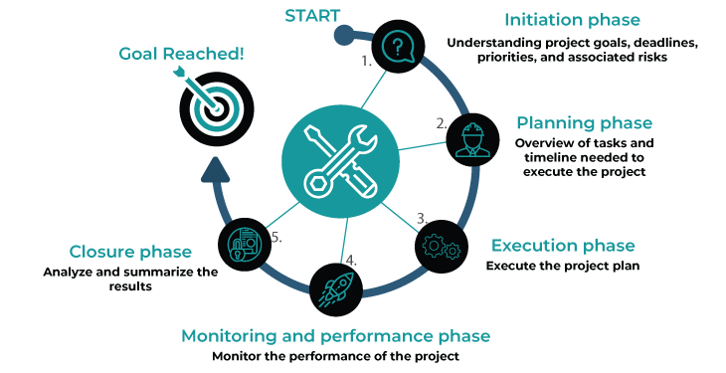
Logistics requires a lot of lead time. It is the time that it takes for a product to be shipped and received. This time is also called shipping lead time, handling lead time, or shipping time. This time is vital for meeting customer demands and improving business productivity. It is an important indicator in inventory management. It can help you understand the costs associated with different parts of your supply chain. Let's examine the most important elements of lead time.
Cost of inventory
It is important to track lead time as well as inventory carrying costs in a supply chain. High levels of either one or both can signify that inventory has become overstocked. In this case, you should adjust order frequency to keep stock moving. Carrying cost is also an important metric to monitor because it is a function of how much a company spends on keeping inventory.
One of the largest components of inventory carrying cost is the cost of capital. It includes the cost of capital used to buy products, plus any interest or loan fees. This can adversely impact cash flow and lead to the need of additional capital. Companies can limit these costs by forecasting their demand for goods and making better purchases. They may also be able to negotiate lower prices with suppliers.
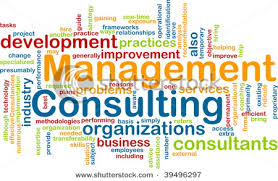
Delivery lead time
The delivery lead time is the time taken between placing an order and receiving it. It must be calculated for every product in a supply chain. The time required to complete a supply chain will depend on how many products the customer has purchased, as well the production capabilities of each individual piece. They will have accumulated each player's lead time by the time the customer reaches the end. It is therefore crucial to accurately measure that time.
The first step in reducing a supply chain's lead time is to identify the critical parts of the process. A company may need to produce custom water bottles for an event. They can cut down on the lead time by identifying which steps take longer than one day. If the manufacturer must produce a certain quantity of water bottles in a single day, they may be able to program a printing system to start the process while the bottles remain being manufactured.
Order lead time
Improving lead times is crucial in managing a supply channel. This can be done by improving the relationships with suppliers and streamlining the ordering process. By placing orders earlier and communicating regularly with suppliers, you can improve order-to delivery. This will decrease the time required to receive orders and increase customer satisfaction.
Lead times will vary depending upon the size of your business. This is because lead times are dependent on the product and how far in advance you place orders. It also depends upon the supplier you use. For example, if you order something on Monday, it could take a week to receive it. If you order it Friday, it could take 4 days to receive it. In order to determine a more accurate lead time, you should calculate each component of the supply chain separately.
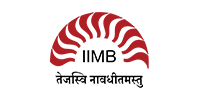
Customer satisfaction
Supply chain components that focus on customer satisfaction and lead times are crucial. Companies should take into consideration the time required to procure items, make them, and then ship them. There are many factors that affect lead times. They may vary from one company to the next. For example, a supplier's lead time may vary from day to day, and the exact amount will depend on the supplier.
To improve customer satisfaction, businesses should measure their performance on key metrics. Measurement of order accuracy, delivery speed, and replacement time can all be important factors. The supply chain of a company is a key factor in determining how satisfied customers are. Analytics can be used to monitor the supply chain and help clients spot problems.
FAQ
How does Six Sigma work
Six Sigma uses statistical analysis for problems to be found, measured, analyzed root causes, corrected, and learned from.
The first step to solving the problem is to identify it.
Next, data will be collected and analyzed to determine trends and patterns.
The problem can then be fixed by taking corrective measures.
The data are then reanalyzed to see if the problem is solved.
This cycle continues until the problem is solved.
What kind of people use Six Sigma
Six-sigma will be well-known to anyone who has worked in operations research or statistics. But anyone can benefit from it.
Because it requires a high degree of commitment, only leaders with strong leadership skills can implement it successfully.
What is the meaning of "project management?"
That is the management of all activities associated with a project.
We include defining the scope of the project, identifying the requirements, preparing the budget, organizing the project team, scheduling the work, monitoring progress, evaluating results, and closing down the project.
What is the role of a manager in a company?
The role of a manager varies from one industry to another.
The manager oversees the day-to-day activities of a company.
He/she makes sure that the company meets its financial obligations, and that it produces goods or services that customers desire.
He/she makes sure that employees adhere to the rules and regulations as well as quality standards.
He/she plans and oversees marketing campaigns.
Statistics
- Hire the top business lawyers and save up to 60% on legal fees (upcounsel.com)
- Our program is 100% engineered for your success. (online.uc.edu)
- This field is expected to grow about 7% by 2028, a bit faster than the national average for job growth. (wgu.edu)
- As of 2020, personal bankers or tellers make an average of $32,620 per year, according to the BLS. (wgu.edu)
- 100% of the courses are offered online, and no campus visits are required — a big time-saver for you. (online.uc.edu)
External Links
How To
How do you use the 5S in your office?
A well-organized workspace will make it easier to work efficiently. A clean desk, a neat room, and a well-organized space are all key factors in ensuring everyone is productive. The five S’s (Sort. Shine. Sweep. Separate. and Store) all work together to ensure that every inch is utilized efficiently and effectively. We'll be going through each step one by one and discussing how they can all be applied in any environment.
-
Sort. Get rid of clutter and papers so you don't have to waste time looking for the right item. This means putting things where you use them most often. If you frequently refer back to something, put it near the place where you look up information or do research. Consider whether you really need the item. If it no longer serves a useful purpose, get rid it!
-
Shine.Keep your belongings neat and orderly so that you spend less time cleaning up after yourself. Anything that could cause harm or damage to others should be thrown out. Find a safe way to store pens that you don't want anyone else to see. It might mean investing in a pen holder, which is a great investment because you won't lose pens anymore.
-
Sweep. Clean off surfaces regularly to prevent dirt from building up on your furniture and other items. To keep surfaces as clean as you can, invest in dusting equipment. You can even set aside a specific area for sweeping and dusting to keep your workstation looking tidy.
-
Separate. Separating your trash into different bins will save you time when you need to dispose of it. To make it easy to dispose of the trash, you will find them strategically placed around the office. Make sure that you take advantage of this location by placing trash bags next to each bin so that you don't have to dig through piles of trash to find what you need.