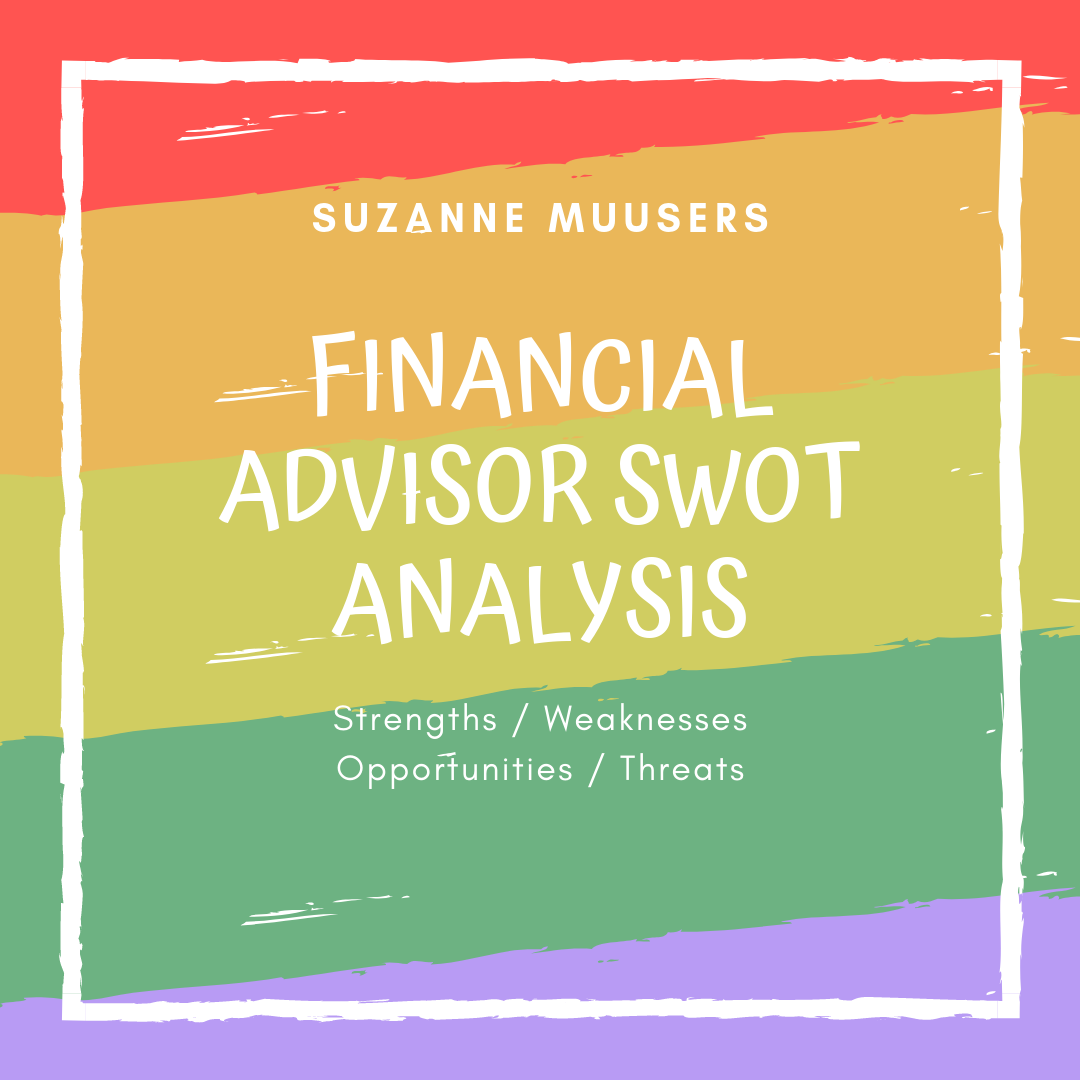
To maintain a healthy work/life harmony, you need to be able to manage your time and organize. This article will help you organize your time and determine your priorities. Prioritization is the key to time management skills. It is also important to plan your tasks and materials. Reward yourself for developing new habits. A new habit is much easier to form if you reward yourself after completing it. This will encourage and motivate you to stick with your new habits. A great habit to develop is the ability to organize your time.
Time management
Priorities are key in managing your time to achieve skill organization. You might find that some tasks are more crucial than others. Others may have closer deadlines. To achieve a long-term goal you may need to finish task A before you can complete task B. Before you start any project, it is important to establish priorities. This will help avoid getting discouraged. A great time management tool is an online calendar that tracks your commitments. There are many apps that can help you plan and track your schedule.
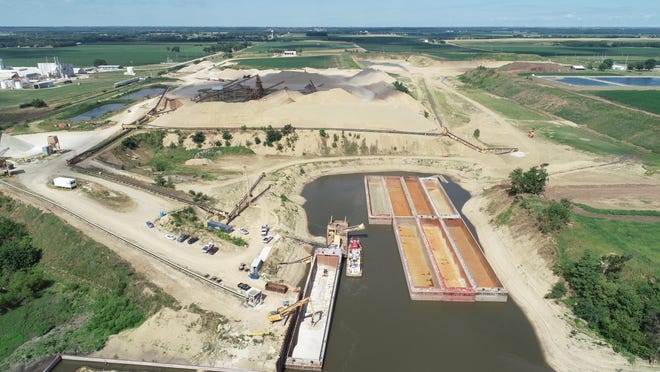
Physical organization
For organizational success, time management skills are vital. These skills include setting realistic deadlines and being disciplined. They also require you to know when tasks are urgent and when they can be put off. This knowledge helps you prioritize your workload. Another kind of organizational skill is physical organisation. This involves keeping your workspace clear of clutter and using the right filing systems. This includes managing your physical resources. If you're not a good organizer, you can try a weekly cleaning session.
Mental organization
Mental organization also includes the ability prioritize assignments. It is essential to be strategic when problem-solving, and anticipate potential issues. Prioritizing also helps reduce stress on a team, especially when there are multiple things to accomplish. Prioritizing does not mean that you only have three items to cross off your list. It's important to understand how to manage time effectively and delegate tasks efficiently. Here are some tips to make the most of your free time.
Prioritization
To prioritise your tasks, you could use a Priority Matrix. This method is also known as the Effort vs. Impact method. Prioritizing your tasks helps you focus more effectively and make your work easier. It is important to prioritise skills that you have. This way, you will have time to work on your most important skills before you move onto the next one.
Documentation
Documentation can save you time, avoid errors, and help you retain information. The average knowledge worker spends about two hours per week searching for information. Effective documentation collects must-know information and organizes it. It reduces time spent searching through email and downloading files. Clear documentation also helps employees stay accountable. This is a win for your business as well as your team. Start by identifying the most commonly used skills in order to build a document system.
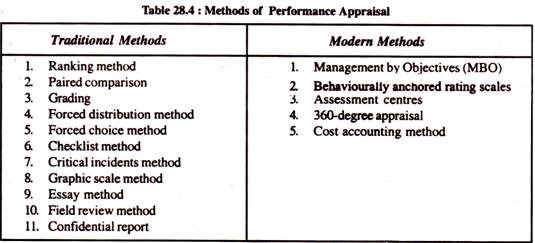
Team management
It is essential to manage your team effectively in order to increase employee engagement. This increased productivity leads to economic benefits and business growth. The management of a team is about bringing together diverse people and managing their skills. Keep the company's overall goals in mind. We'll be discussing some key components of effective team management in the next paragraphs. We will also discuss the various skills required to manage a group.
FAQ
How can a manager motivate employees?
Motivation refers to the desire to perform well.
Engaging in something fun can be a great way to get motivated.
Or you can get motivated by seeing yourself making a contribution to the success of the organization.
If you are a doctor and want to be one, it will likely be more rewarding to see patients than to read medical books every day.
A different type of motivation comes directly from the inside.
Perhaps you have a strong sense to give back, for example.
You may even find it enjoyable to work hard.
If you don’t feel motivated, find out why.
You can then think of ways to improve your motivation.
How do you define Six Sigma?
Six sigma is a common concept for people who have worked in statistics or operations research. But anyone can benefit from it.
Because it requires a high degree of commitment, only leaders with strong leadership skills can implement it successfully.
What is Six Sigma?
It's a method for quality improvement that focuses on customer service as well as continuous learning. The goal is to eliminate defects by using statistical techniques.
Six Sigma was developed at Motorola in 1986 as part of its efforts to improve manufacturing processes.
The idea quickly spread in the industry. Many organizations today use six-sigma methods to improve product design and production, delivery and customer service.
Statistics
- The average salary for financial advisors in 2021 is around $60,000 per year, with the top 10% of the profession making more than $111,000 per year. (wgu.edu)
- This field is expected to grow about 7% by 2028, a bit faster than the national average for job growth. (wgu.edu)
- 100% of the courses are offered online, and no campus visits are required — a big time-saver for you. (online.uc.edu)
- Our program is 100% engineered for your success. (online.uc.edu)
- As of 2020, personal bankers or tellers make an average of $32,620 per year, according to the BLS. (wgu.edu)
External Links
How To
What is Lean Manufacturing?
Lean Manufacturing is a method to reduce waste and increase efficiency using structured methods. They were created by Toyota Motor Corporation in Japan in the 1980s. It was designed to produce high-quality products at lower prices while maintaining their quality. Lean manufacturing seeks to eliminate unnecessary steps and activities in the production process. It has five components: continuous improvement and pull systems; just-in time; continuous change; and kaizen (continuous innovation). The production of only what the customer needs without extra work is called pull systems. Continuous improvement means continuously improving on existing processes. Just-in–time refers when components or materials are delivered immediately to their intended destination. Kaizen is continuous improvement. This can be achieved by making small, incremental changes every day. Fifth, the 5S stand for sort, set up in order to shine, standardize, maintain, and standardize. These five elements are combined to give you the best possible results.
Lean Production System
The lean production system is based on six key concepts:
-
Flow - focuses on moving information and materials as close to customers as possible.
-
Value stream mapping: This is a way to break down each stage into separate tasks and create a flowchart for the entire process.
-
Five S’s - Sorted, In Order. Shine. Standardize. And Sustain.
-
Kanban – visual signals like colored tape, stickers or other visual cues are used to keep track inventory.
-
Theory of constraints: Identify bottlenecks and use lean tools such as kanban boards to eliminate them.
-
Just-in Time - Send components and material directly to the point-of-use;
-
Continuous improvement - incremental improvements are made to the process, not a complete overhaul.