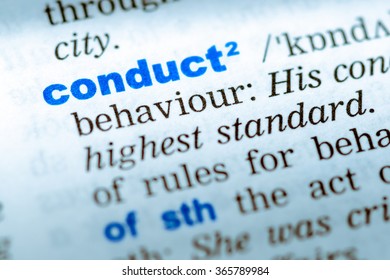
Waste management has a long tradition. The first collection vehicles were open-backed wagons powered by horses. The first motorized versions of these collection vehicles were introduced in the early 20th-century. Later, closed-top trucks were introduced which helped reduce odours and provided a convenient way to dump refuse. The Garwood Load Packer truck featured a hydraulic compactor in the 1920s. This innovation allowed the truck to take on more rubbish per route. Later, waste-to-energy was developed and the modern bin lorries were born. In the twentieth century, recycling was also introduced.
Incinerators
Incineration is a waste management process that makes energy by burning waste materials. The resulting heat is used to generate steam, which can drive a turbine that produces electricity. Incineration plants typically produce two-thirds a megawatt hour of electricity per ton of municipal waste. District heating can also be made from this process. A single plant is capable of burning 600 metric tones of waste per day and producing about 1 ton of Ash per Day.
Nottingham was home to the first ever incinerator built in Britain in 1874. Incinerators were later built all over the country. Many cities had their own destructions. The electricity generated by burning rubbish powered electric refuse collection vehicles and sewer pumps.
Dust-yards
The first municipal solid waste management system was the "dust-yard" system. It was an early 19th-century London invention. This innovative approach was based upon the monetary value household waste. It also included coal ash from domestic fireplaces. This material was desired by many industries, including the brick and agricultural. This material was highly valued and dust-contractors were encouraged to fully recover their residual waste. This method was a success and helped smoothen the transition to England's public solid waste services.
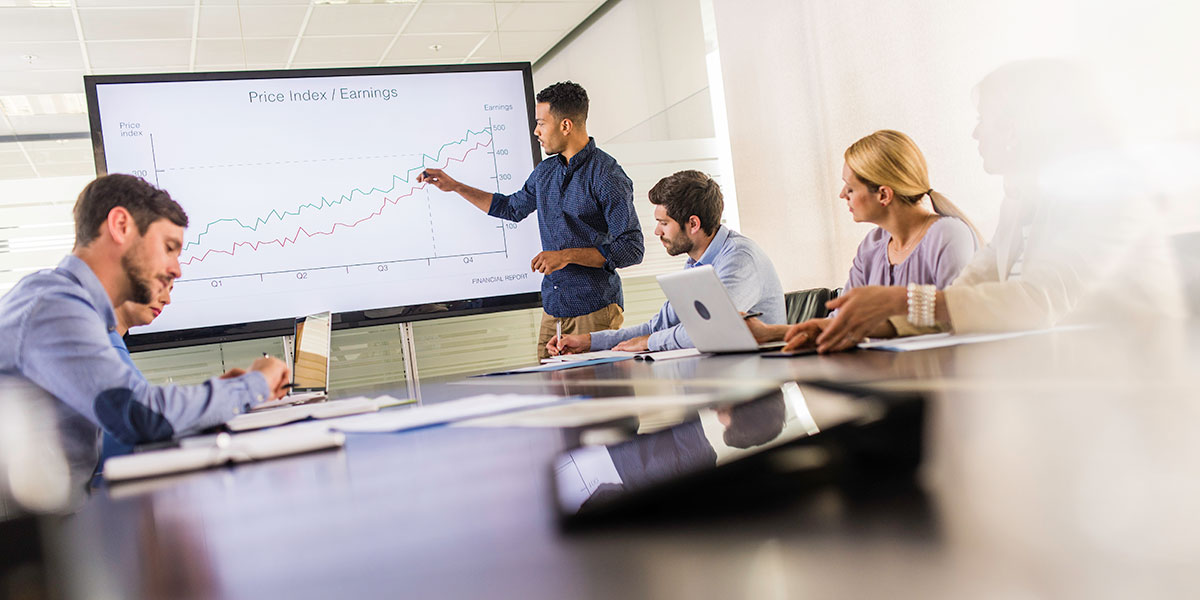
Around 1850, the first waste collection system was established. A dust-yard, also called an ash-pit, was the common way for people to dispose off their waste. A crew of two men collected this waste. One man was called a filler and he shoveled the waste into a container from the dust-pit. The other man, who is known as a transporter, carried the basket onto a cart. The process was repeated until all the contents were loaded onto the cart. The cart was then returned to the dust-yard and passed through a chute. Its contents were then dropped onto the dust heap.
Inflated reserves
Inflation and high labor costs can both increase the cost of services in the environment. Companies should report the depreciation cost in their financial statements to avoid such high costs. This could lead to an increase in reserves for waste management companies. A company must also record the cost for abandoned or failed landfill development plans.
In 1997, Waste Management's CEO noticed some irregularities and requested a full review of its accounts. An investigation found that $1.7 billion had been missed in the company's financial statements. The scandal caused the stock price to fall by around a third.
Accounting fraud
The Securities and Exchange Commission found a massive accounting fraud at Waste Management this past year. According to the SEC, former Waste Management executives lied about their company's financial performance and inflated profits by up to $1.7 billion. As a result, the company was forced to settle a class action lawsuit and pay $7 million in a civil fine.
Waste Management used accounting techniques that were contrary to generally accepted accounting rules in order to conceal the fraud. The practices included deferring expenses, erasing current expenses, and using other techniques to bury expenses. Waste Management's principal fixed asset was garbage trucks and containers. Therefore, the depreciation expenses for these assets were substantial and easy to manipulate.
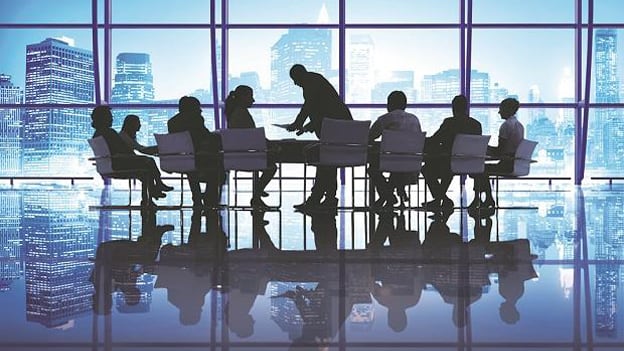
Harvest Power
Harvest Power, a new business model that diverts organic waste away from landfills, transforms it into multiple streams of value. This reduces net greenhouse gas emissions, lowers total disposal costs, and slows landfill space consumption. It also returns unutilized inputs from agriculture into renewable energy. Harvest Power uses this system to promote renewable energy policies and reduce landfill space.
Harvest Power has been a huge success in Spain, Germany and its investors believe that the model could be applied to the United States. It raised $110,000,000 in funding in 2012, which included funds from Al Gore's Generation Investment Management (GIM) and Kleiner Perkins. Waste Management, the largest trash processing company in the country, has also invested. They have pledged to eliminate all landfills.
FAQ
Six Sigma is so popular.
Six Sigma is simple to implement and can yield significant results. Six Sigma provides a framework to measure improvements and allows companies to focus on the most important things.
How do you manage employees effectively?
Effectively managing employees means making sure they are productive and happy.
This also involves setting clear expectations and monitoring their performance.
Managers need clear goals to be able to accomplish this.
They need to communicate clearly and openly with staff members. They must communicate clearly with staff members.
They will also need to keep records about their team's activities. These include:
-
What did you accomplish?
-
How much work did you put in?
-
Who did it?
-
When it was done?
-
Why it was done?
This information can be used to monitor performance and evaluate results.
What are the main management skills?
Any business owner needs to be able to manage people, finances, resources and time. These skills include the ability of managing people, finances, time, space, and other factors.
You will need management skills to set goals and objectives, plan strategies, motivate employees, resolve problems, create policies and procedures, and manage change.
You can see that there are many managerial duties.
What is a management tool to help with decision-making?
A decision matrix, a simple yet powerful tool for managers to make decisions, is the best. It allows them to consider all possible solutions.
A decision matrix represents alternatives in rows and columns. This makes it easy to see how each alternative affects other choices.
In this example, we have four possible alternatives represented by the boxes on the left side of the matrix. Each box represents one option. The top row displays the current situation, and the bottom row shows what might happen if nothing is done.
The middle column shows the effect of choosing Option 1. In this case, it would mean increasing sales from $2 million to $3 million.
These are the results of selecting Options 2 or 3. These are both positive changes that increase sales by $1million and $500,000. But, they also have some negative consequences. Option 2 increases the cost of goods by $100,000. Option 3 decreases profits and makes them less attractive by $200,000.
Finally, the last column shows the results of choosing Option 4. This would result in a reduction of sales of $1 million.
The best part of using a decision-matrix is that it doesn't require you to know which numbers belong where. You can just glance at the cells and see immediately if one given choice is better.
The matrix has already done all of the work. It's simply a matter of comparing the numbers in the relevant cells.
Here's a sample of how you might use decision matrixes in your business.
It is up to you to decide whether to spend more money on advertising. By doing so, you can increase your revenue by $5 000 per month. However, additional expenses of $10 000 per month will be incurred.
You can calculate the net result of investing in advertising by looking at the cell directly below the one that says "Advertising." That number is $15 thousand. Advertising is worth much more than the investment cost.
What are the four major functions of Management?
Management is responsible for planning, organizing, directing, and controlling people and resources. It also includes developing policies and procedures and setting goals.
Management is the ability to direct, coordinate, control, motivate, supervise, train, and evaluate an organization's efforts towards achieving its goals.
These are the four major functions of management:
Planning - Planning refers to deciding what is needed.
Organizing - Organizing involves deciding how things should be done.
Directing - This refers to getting people follow instructions.
Controlling - This is the ability to control people and ensure that they do their jobs according to plan.
What are some common mistakes managers make when managing people?
Sometimes managers make it harder for their employees than is necessary.
They may not delegate enough responsibilities and not provide sufficient support.
Many managers lack the communication skills to motivate and lead their employees.
Some managers set unrealistic expectations for their staff.
Some managers may try to solve every problem themselves instead of delegating responsibility to others.
Statistics
- This field is expected to grow about 7% by 2028, a bit faster than the national average for job growth. (wgu.edu)
- Our program is 100% engineered for your success. (online.uc.edu)
- Your choice in Step 5 may very likely be the same or similar to the alternative you placed at the top of your list at the end of Step 4. (umassd.edu)
- The average salary for financial advisors in 2021 is around $60,000 per year, with the top 10% of the profession making more than $111,000 per year. (wgu.edu)
- Hire the top business lawyers and save up to 60% on legal fees (upcounsel.com)
External Links
How To
How do I get my Six Sigma certification?
Six Sigma is a tool for quality management to improve processes and increase efficiency. It's a methodology that helps companies achieve consistent results from their operations. The name derives its meaning from the "sigmas" Greek word, which is composed of two letters that mean six. Motorola was the first to develop this process. Motorola realized they needed to standardize the manufacturing processes to produce products faster and cheaper. The many people involved in manufacturing had caused problems with consistency. To resolve this issue, they used statistical tools like Pareto analysis and control charts. After this, they would apply these techniques to every part of the operation. They would then be able make improvements where needed. There are three main steps to follow when trying to get your Six Sigma certification. First, you need to determine if your qualifications are valid. Before you can take any tests, you will need to take some classes. After passing the classes, you will be able to take the tests. It is important to review everything that you have learned in class. Once you have completed the class, you will be ready for the test. If you pass, then you will become certified. Finally, you will be able add your certifications onto your resume.