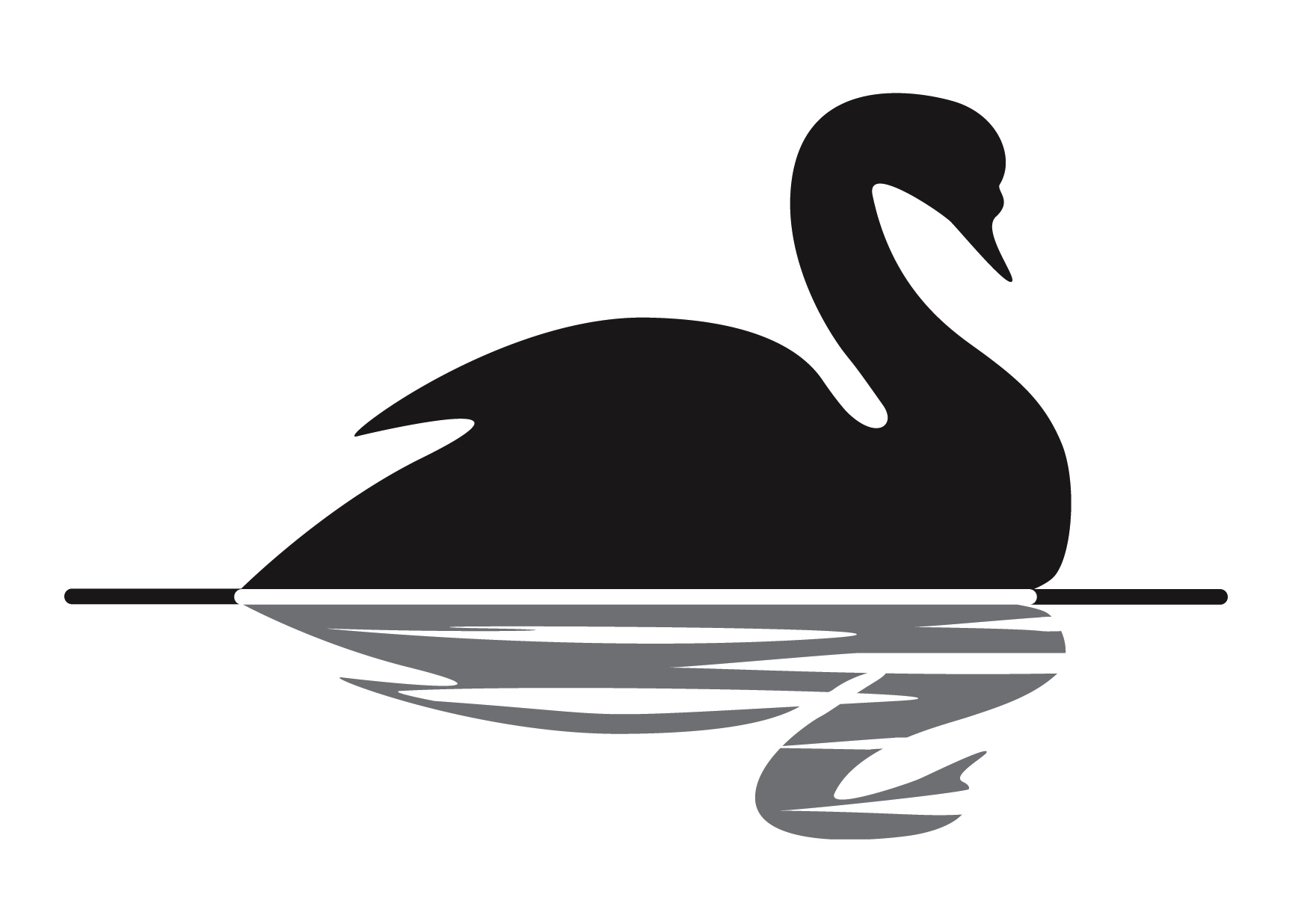
To be considered a PSM program, a company must comply with 14 elements. These elements include Permissible exposure limits (Perhazard analyses), Physical data and Corrosivity data. These elements are crucial to the success of a PSM Program. A PSM program that complies with these requirements will be considered compliant. These elements should be followed by your company.
Analyses for process hazards
A process hazard assessment is an essential component of a safety management plan. It helps to identify potential hazards, and the consequences of their failure. This analysis must be done with a group of people who are familiar with the process. It will also include information about human factors and past incidents. The analysis must be reviewed every five years after it is completed. Hazard analysis must be used as part of safety management systems.
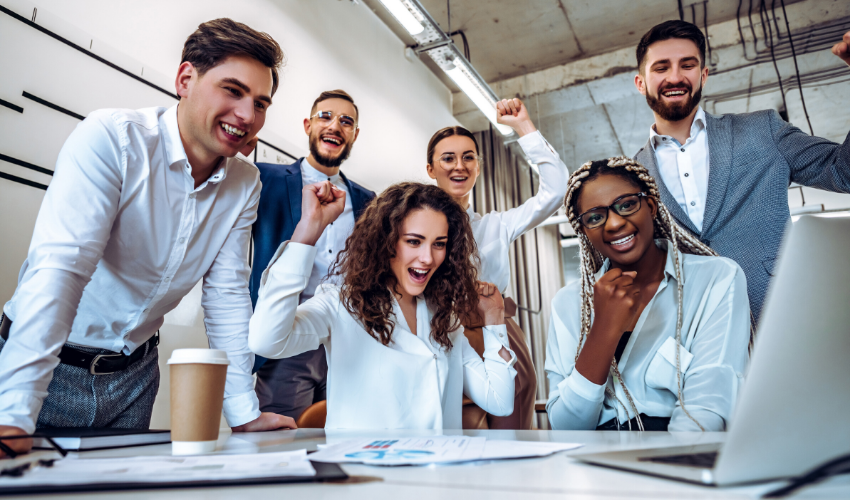
Permissible exposure limits
OSHA Process Safety Management Standard is a set standards that govern processes that involve hazardous chemicals, gases, or fluids. This standard is applicable to businesses that make or process hazardous chemicals. It does NOT apply to hydrocarbon fuels solely used at work, to retail or to oil and gas well-drilling. It also does not apply for facilities that are usually unoccupied or far away.
Physical data
PSM refers to the analysis and control of the risks associated with hazardous products and materials. This means knowing how to safely handle, transport and store hazardous substances. This will result in less product waste and fewer workplace injuries. It facilitates decision-making and helps organizations prioritize safety and health. PSM is a vital part of a safe workplace. It can help companies prevent costly medical emergencies and save money.
Data on corrosivity
The PSM standard outlines requirements for handling chemicals and other substances that could cause damage to buildings or equipment. The PSM also includes requirements for emergency action plans and permit systems, and requires periodic compliance audits. PSM-compliant workplaces will provide safety and protection for employees, no matter how hazardous your organization's production processes are.
Data on thermal stability
OSHA has developed a standard for collecting and reporting PSM thermal stability data. This program will help researchers be aware of potential hazards and reduce the risk of accidental releases. It will be constantly reviewed and revised to accommodate new research projects. It will be made available to all employees. The PSM program includes information on toxicity, reactivity, corrosivity, and physical properties.
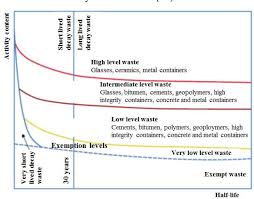
Employee participation clause
Process Safety Management, also known as Process Safety Management, is a methodical analytical approach to preventing accidents that are caused by hazardous chemicals (HHC). It is an important step in improving process safety and must be implemented at all levels, including maintenance and production. It contains 14 elements that should be implemented, including employee participation clauses. Below are just a few examples.
FAQ
What are your main management skills
No matter if they are running a local business or an international one, management skills are vital. They include the ability to manage people, finances, resources, time, and space, as well as other factors.
Management Skills are also needed when you're setting goals and objectives, planning strategies, leading teams, motivating employees, resolving problems, creating policies and procedures, and managing change.
As you can see there is no end to the number of managerial tasks.
What are management concepts?
Management concepts are the fundamental principles and practices that managers use when managing people and their resources. These include topics such as human resource policies and job descriptions, performance assessments, training programs and employee motivation.
What are some common mistakes managers make?
Sometimes managers make their job harder than they need to.
They may not delegate enough responsibilities to staff and fail to give them adequate support.
Many managers lack the communication skills to motivate and lead their employees.
Some managers set unrealistic expectations for their staff.
Managers might try to solve every problem by themselves rather than delegating the responsibility.
How do you manage employees effectively?
Effectively managing employees requires that you ensure their happiness and productivity.
It is important to set clear expectations about their behavior and keep track of their performance.
Managers must be clear about their goals and those of their teams in order to succeed.
They need to communicate clearly and openly with staff members. They need to communicate clearly with their staff.
They must also keep records of team activities. These include:
-
What was accomplished?
-
How much work did you put in?
-
Who did it?
-
Was it done?
-
Why did it happen?
This information can help you monitor your performance and to evaluate your results.
Why does it sometimes seem so hard to make good business decisions
Businesses are complex systems, and they have many moving parts. They require people to manage multiple priorities and deal with uncertainty and complexity.
Understanding how these factors impact the whole system is key to making informed decisions.
It is important to consider the functions and reasons for each part of the system. It is important to then consider how the individual pieces relate to each other.
It is also worth asking yourself if you have any unspoken assumptions about how you have been doing things. If they don't, you may want to reconsider them.
For help, ask someone else if you're still stumped after all the above. They may see things differently from you and have insights that could help you find a solution.
What is TQM?
The industrial revolution saw the realization that prices alone were not sufficient to sustain manufacturing companies. This led to the birth of quality. If they wanted to stay competitive, they needed to improve their quality and efficiency.
Management responded to the need to improve, and developed Total Quality Management (TQM). This focused on improving every aspect of an organization’s performance. It included continuous improvement processes, employee involvement, and customer satisfaction.
Statistics
- As of 2020, personal bankers or tellers make an average of $32,620 per year, according to the BLS. (wgu.edu)
- The average salary for financial advisors in 2021 is around $60,000 per year, with the top 10% of the profession making more than $111,000 per year. (wgu.edu)
- 100% of the courses are offered online, and no campus visits are required — a big time-saver for you. (online.uc.edu)
- Our program is 100% engineered for your success. (online.uc.edu)
- This field is expected to grow about 7% by 2028, a bit faster than the national average for job growth. (wgu.edu)
External Links
How To
What is Lean Manufacturing?
Lean Manufacturing is a method to reduce waste and increase efficiency using structured methods. They were developed by Toyota Motor Corporation in Japan during the 1980s. It was designed to produce high-quality products at lower prices while maintaining their quality. Lean manufacturing eliminates unnecessary steps and activities from a production process. It is made up of five elements: continuous improvement, continuous improvement, just in-time, continuous change, and 5S. It is a system that produces only the product the customer requests without additional work. Continuous improvement is constantly improving upon existing processes. Just-in–time refers when components or materials are delivered immediately to their intended destination. Kaizen means continuous improvement. Kaizen involves making small changes and improving continuously. Last but not least, 5S is for sort. To achieve the best results, these five elements must be used together.
Lean Production System
Six key concepts underlie the lean production system.
-
Flow: The goal is to move material and information as close as possible from customers.
-
Value stream mapping is the ability to divide a process into smaller tasks, and then create a flowchart that shows the entire process.
-
Five S's, Sort, Set in Order, Shine. Standardize. and Sustain.
-
Kanban: Use visual signals such stickers, colored tape, or any other visual cues, to keep track your inventory.
-
Theory of constraints - identify bottlenecks in the process and eliminate them using lean tools like kanban boards;
-
Just-intime - Order components and materials at your location right on the spot.
-
Continuous improvement: Make incremental improvements to the process instead of overhauling it completely.