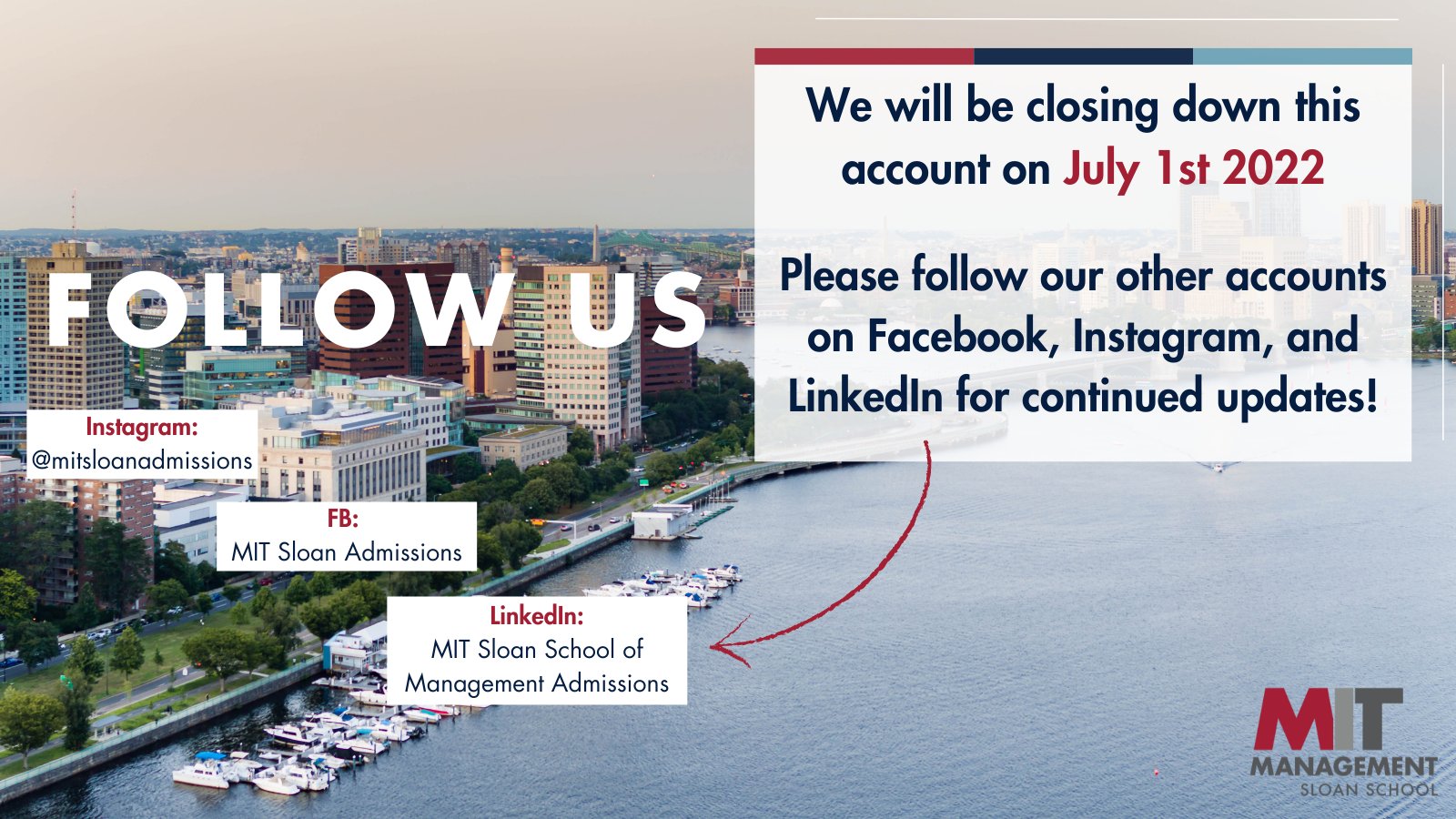
Forecasting based upon ANN
Artificial neural networks (ANNs), which are widely used in forecasting, can be found all over the world. Various techniques have been created to make ANNs more accurate. A new research aims to apply ANNs to Supply Chain Management. This research compares the performance between four different ANN types: the FSANN FWANN, HYANN and HYANN. HYANN is a combination of FWANN and FSANN, which incorporates feature selection and feature weighting to improve performance.
Neural networks are composed of many interconnected layers. Each layer contains a number of neurons. The input layer is responsible for receiving external data and the output layer provides results. The hidden layer also contains neurons, which are used to refine results. While the number or neurons in the input layers and output layers is predetermined, the hidden layer may contain a variety of neurons. It is dependent on the number and location of hidden layers, existence of bias neurons, as well as the rate of learning.
Probabilistic forecasting
Probabilistic Forecasting can be applied to many supply chain management issues. Its main focus is to reduce uncertainty in making decisions. It is important to consider all the sources of uncertainty, including those that are not readily measurable. This approach will help companies plan for their inventory.

A probabilistic forecast involves creating different scenarios for different outcomes. It may include uncertainties like uncertain demand, uncertain lead time, and unanticipated return from customers. It may also include uncertainty around the delivery date of an order to a supplier. It is possible to assess the uncertainty involved in these scenarios manually by having a detailed understanding of the context.
Regression analysis
Supply chain management forecasting can be difficult, but regression analysis can help. It forces businesses to analyze actual data. If a company wants to know the rainy season, they can plot sales versus rainfall for the past three years. This will enable them to compare sales peaking visually.
A statistical model is needed to forecast the demand for a product. It must be based on historical data. The model is then refined through the addition of current data and testing with historical data. The forecasting model is then used to predict future trends. Supply chain managers must be aware that forecasting models for supply chain management have certain limitations.
AI
AI is a disruptive technology that can help supply chain managers anticipate future needs, and it can also reduce processing time. AI also allows for smarter decision-making. It provides valuable insights into market trends, weather patterns, and other variables. This data can make a real difference in customer relationships and the credibility of an industry. It can help companies to understand the causes and whereabouts of bottlenecks.
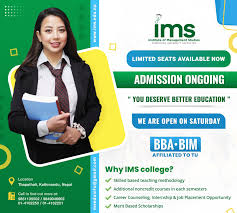
AI forecasting can help improve supply chain management and logistics operations, reducing costs and boosting profit margins. It can optimize the forecasting process by analysing historical data as well as current trends, like social media chatter. AI can analyze this data to aid logistics operators in determining demand throughout the supply chain.
FAQ
What role should a manager play within a company
Each industry has a different role for a manager.
In general, a manager controls the day-to-day operations of a company.
He/she ensures the company meets its financial commitments and produces goods/services that customers demand.
He/she ensures that employees follow the rules and regulations and adhere to quality standards.
He/she plans new products and services and oversees marketing campaigns.
What is Six Sigma and how can it help you?
It's a method for quality improvement that focuses on customer service as well as continuous learning. The goal is to eradicate defects through statistical techniques.
Six Sigma was developed at Motorola in 1986 as part of its efforts to improve manufacturing processes.
It was quickly adopted by the industry and many companies are now using six-sigma to improve product design, production, delivery, customer service, and product design.
What is Six Sigma?
Six Sigma uses statistical analyses to locate problems, measure them, analyze root cause, fix problems and learn from the experience.
The first step is identifying the problem.
Next, data will be collected and analyzed to determine trends and patterns.
Then corrective actions are taken to solve the problem.
Final analysis of data is done to determine if the problem has been solved.
This continues until you solve the problem.
How does a manager develop his/her management skills?
By practicing good management skills at all times.
Managers must continuously monitor the performance levels of their subordinates.
You should immediately take action if you see that your subordinate is not performing as well as you would like.
You must be able to spot what is lacking and how you can improve it.
What is the difference between a project and a program?
A project is temporary; a program is permanent.
Projects usually have a goal and a deadline.
It is usually done by a group that reports back to another person.
A program usually has a set of goals and objectives.
It is often implemented by one person.
Why is it so hard to make smart business decisions?
Complex business systems have many moving parts. The people who run them must juggle multiple priorities at once while also dealing with uncertainty and complexity.
To make good decisions, you must understand how these factors affect the entire system.
To do this, you must think carefully about what each part of the system does and why. You then need to consider how those individual pieces interact with each other.
Ask yourself if there are hidden assumptions that have influenced your behavior. You might consider revisiting them if they are not.
If you're still stuck after all this, try asking someone else for help. You might find their perspective is different from yours and they may have insight that can help you find the solution.
Statistics
- Hire the top business lawyers and save up to 60% on legal fees (upcounsel.com)
- 100% of the courses are offered online, and no campus visits are required — a big time-saver for you. (online.uc.edu)
- Your choice in Step 5 may very likely be the same or similar to the alternative you placed at the top of your list at the end of Step 4. (umassd.edu)
- This field is expected to grow about 7% by 2028, a bit faster than the national average for job growth. (wgu.edu)
- The BLS says that financial services jobs like banking are expected to grow 4% by 2030, about as fast as the national average. (wgu.edu)
External Links
How To
How do you implement a Quality Management Plan (QMP)?
QMP, which was introduced by ISO 9001:2008, is a systematic approach to improving products, services, and processes through continuous improvement. It helps to improve customer satisfaction and product/service quality by continuously measuring, analyzing, controlling and improving.
The QMP is a standard method used to ensure good business performance. QMP helps improve production, service delivery and customer relationships. QMPs should address all three dimensions: Products, Services, and processes. A "Process" QMP is one that only includes one aspect. When the QMP focuses on a Product/Service, it is known as a "Product" QMP. And when the QMP concentrates on Customer Relationships, it is called "Customer" QMP.
When implementing a QMP, there are two main elements: Scope and Strategy. They are defined as follows:
Scope: This defines what the QMP will cover and its duration. For example, if you want to implement a QMP that lasts six months, then this scope will outline the activities done during the first six.
Strategy: This describes the steps taken towards achieving the goals set forth in the scope.
A typical QMP includes five phases: Design, Planning, Development and Implementation. Each phase is explained below:
Planning: This stage identifies and prioritizes the QMP's objectives. To understand the expectations and requirements of all stakeholders, the project is consulted. Next, you will need to identify the objectives and priorities. The strategy for achieving them is developed.
Design: This stage is where the design team creates the vision, mission and strategies necessary for successful implementation of QMP. These strategies are executed by creating detailed plans.
Development: This is where the development team works to build the capabilities and resources necessary for the successful implementation of the QMP.
Implementation is the actual implementation of QMP according to the plans.
Maintenance: This is an ongoing procedure to keep the QMP in good condition over time.
Additionally, the QMP should include additional items:
Participation of Stakeholders: The QMP's success depends on the participation of stakeholders. They must be involved in all phases of the QMP's development, planning, execution, maintenance, and design.
Initiation of a Project: A clear understanding and application of the problem statement is crucial for initiating a project. In other words, the initiator needs to know why they want to do something and what they expect from the outcome.
Time frame: It is crucial to know the time frame for the QMP. For a short time, you can start with the simple version of the QMP. For a long-term commitment you may need more complicated versions.
Cost Estimation is another important aspect of the QMP. Planning is not possible without knowing the amount of money you will spend. Therefore, cost estimation is essential before starting the QMP.
QMPs should not be considered a static document. It evolves as the company grows and changes. It is important to review it periodically to ensure it meets all current requirements.