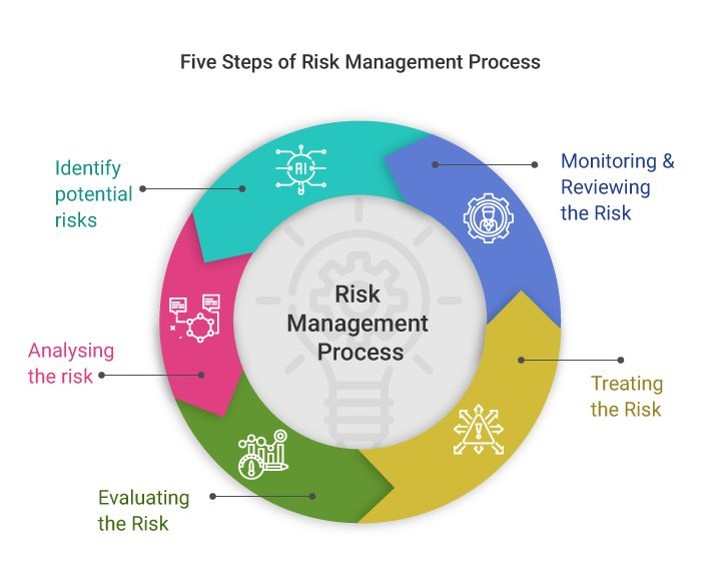
Logistics refers to the movement of goods from production to final delivery. The logistics industry involves many organizations, people, activities, and information to make goods available for purchase. A logistics supply-chain is a collaborative effort among multiple stakeholders. Although many companies are focused on logistics, there is a lot more to the process than just logistics. Here are some examples of different logistical systems. Learn more about these systems to improve your company's supply chains operations.
Logistics is the movement and storage of goods from their initial production through final delivery.
Logistics refers the efficient movement, storage and delivery of products from production through to delivery. By optimizing flow, products can reach their customers at a precise time, at the best place, and at a reasonable cost. The following are 7 "rights" of logistics. The first is to arrive at the right time. Products should be delivered to customers on time, without delay, in the right condition.
Inbound logistics focuses on the inbound movement of materials and products to manufacturers, whereas outbound logistics focuses on the outbound flow of goods and information from sources outside of the business. Inbound logistics focuses on acquiring materials and arranging inbound transportation, storage, and distribution to customers. Reverse logistics is the return shipment and packaging of finished products. It also includes the management of remaining inventory and, in certain cases, the disposal and reuse of waste.
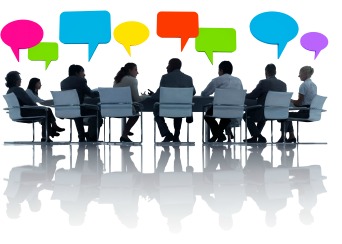
It is a risk-adjusted business
A risk-adjusted investor (RAR) is a type of investment that involves capital or funds that are more risky than normal business investments. The opportunity cost of risk is the difference between risk-adjusted and normal business investment yields. RAR can be used to reduce risk in investments and help business owners manage their cash flow across all functional areas.
It is a small portion of a larger supply chain that works together
A highly integrated supply chain is a highly interdependent network of suppliers that rely on timely deliveries of quality components. In such a chain, failure to deliver could bring the whole chain to a halt. Even the best suppliers and logistics providers cannot prevent every disruption. To ensure that every participant in the chain functions smoothly and efficiently, it's important to evaluate the risks involved in each system.
Manufacturers and retailers can collaborate to benefit both sides. One example of this is a recent partnership between a retailer with a major U.S. chain retail store. It resulted in lower logistics costs between the factory's warehouse and the store. Retailers can also benefit from collaborations in this field to increase their sales. In this area, retailers and manufacturers can cooperate to reduce transport and labor expenses between the factory-store location.
It involves software
Companies can manage their entire supply chain by using supply management software. The software handles all aspects of the supply chain, from vendor relationships to transactions. Supply chain management software should be used regardless of whether you run a small business or large corporation. These programs can be used to manage inventory, supplier relationships, data flow, and other business functions. These programs can include all phases of product development, such as warehousing or shipping. They might also manage inventory and offer insight into trends or demand.
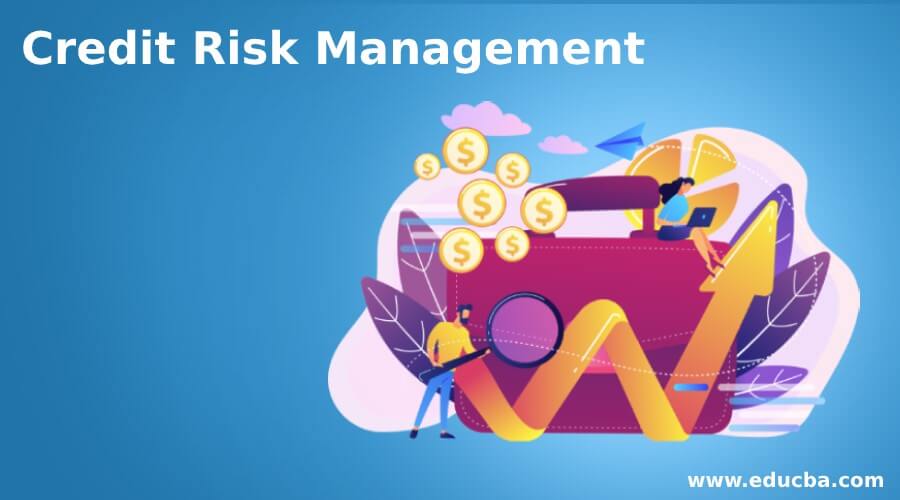
Software for logistics management can improve inventory management, real time fleet management, and streamline communication. It can also increase customer service. It automates day-to-day tasks and gives business owners actionable insights. It can also improve inventory and communication processes, which are crucial to successful management of supply chains. These software can be used to improve customer service, and increase profitability. You may be interested in the potential benefits of software purchase for your company.
FAQ
What are some common management mistakes?
Sometimes managers make it harder for their employees than is necessary.
They may not be able to delegate enough responsibility to staff or provide adequate support.
Additionally, many managers lack communication skills that are necessary to motivate and direct their teams.
Some managers set unrealistic expectations for their staff.
Managers may prefer to solve every problem for themselves than to delegate responsibility.
How do you manage employees effectively?
Effectively managing employees requires that you ensure their happiness and productivity.
This includes setting clear expectations for their behavior and tracking their performance.
Managers must set clear goals for their employees and themselves to achieve this goal.
They should communicate clearly to staff members. They should also ensure that they both reward high performers and discipline those who are not performing to their standards.
They must also keep track of the activities of their team. These include:
-
What was the result?
-
How much work were you able to accomplish?
-
Who did it?
-
It was done!
-
Why?
This information can be used to monitor performance and evaluate results.
What is Six Sigma and how can it help you?
It is a way to improve quality that places emphasis on customer service and continuous learning. The goal is to eliminate defects by using statistical techniques.
Motorola created Six Sigma as part of their efforts to improve manufacturing processes in 1986.
The idea spread quickly in the industry. Today many organizations use six-sigma techniques to improve product design.
How does Six Sigma function?
Six Sigma uses statistical analyses to locate problems, measure them, analyze root cause, fix problems and learn from the experience.
The first step is to identify the problem.
The next step is to collect data and analyze it in order to identify trends or patterns.
The problem can then be fixed by taking corrective measures.
Finally, the data are reanalyzed in order to determine if it has been resolved.
This continues until the problem has been solved.
Statistics
- The average salary for financial advisors in 2021 is around $60,000 per year, with the top 10% of the profession making more than $111,000 per year. (wgu.edu)
- Your choice in Step 5 may very likely be the same or similar to the alternative you placed at the top of your list at the end of Step 4. (umassd.edu)
- As of 2020, personal bankers or tellers make an average of $32,620 per year, according to the BLS. (wgu.edu)
- Hire the top business lawyers and save up to 60% on legal fees (upcounsel.com)
- Our program is 100% engineered for your success. (online.uc.edu)
External Links
How To
How can you implement the Kaizen technique?
Kaizen means continuous improvement. The term was coined in the 1950s at Toyota Motor Corporation and refers to the Japanese philosophy emphasizing constant improvement through small incremental changes. It is a process where people come together to improve their processes.
Kaizen is one of Lean Manufacturing's most efficient methods. Employees responsible for the production line should identify potential problems in the manufacturing process and work together to resolve them. This will increase the quality and decrease the cost of the products.
Kaizen is an approach to making every worker aware and alert to what is happening around them. It is important to correct any problems immediately if they are discovered. If someone is aware of a problem at work, he/she should inform his/her manager immediately.
When doing kaizen, there are some principles we must follow. Start with the end product, and then move to the beginning. For example, if we want to improve our factory, we first fix the machines that produce the final product. We then fix the machines producing components, and the machines producing raw materials. Then we fix the workers, who directly work with these machines.
This method, called 'kaizen', focuses on improving each and every step of the process. Once we have finished fixing the factory, we return to the beginning and work until perfection.
How to measure kaizen's effectiveness in your business is essential to implement it. There are several ways to determine whether kaizen is working well. Another method is to see how many defects are found on the products. Another way is to see how much productivity has increased since implementing kaizen.
If you want to find out if your kaizen is actually working, ask yourself why. You were trying to save money or obey the law? It was a way to save money or help you succeed.
If you answered yes to any one of these questions, congratulations! You are now ready to begin kaizen.