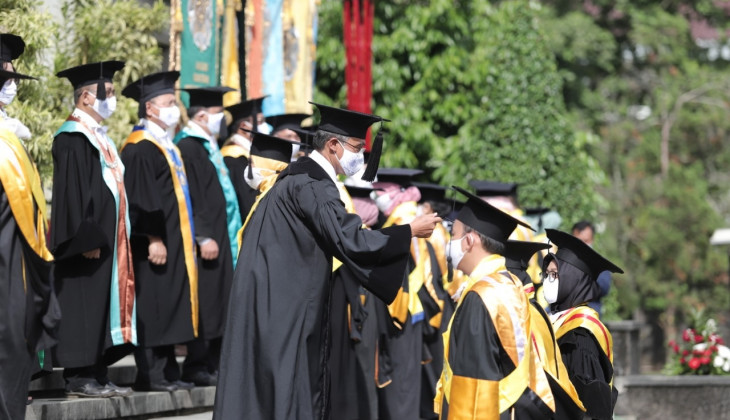
Extending the supply chain is the next step in healthcare delivery. The supply chain must reach beyond the hospital walls. It must also include last-mile transportation. Telemedicine, at home testing kits, and Telehealth will all require that the healthcare supply chain extends beyond the hospital. This article examines some of the key indicators for a healthy supply network.
Indicators of supply chain performance
As the supply chain plays a vital role in healthcare facilities, the need to monitor and manage this part of the healthcare process is paramount. Key Performance Indicators or KPIs are an excellent tool that can help track progress and improve internal decision-making. KPIs may be used by anyone in the organisation, even nurses and doctors. This paper aims to identify and validate KPIs for healthcare and examine their relative importance.
Supply chains' success in healthcare is dependent on their support for patient care. Supply chain managers provide data that hospitals can use to improve patient care. They can enhance patient safety by ensuring efficient treatment.
The reliability of the supply chain
Reliability and security are two of the most critical aspects for logistics in healthcare. This reliability can depend on the context and be crucial in meeting patient requirements and maintaining continuity of care. A reliable supply chain is crucial to the continuous flow of patients and services to hospitals, clinics, and other medical facilities.
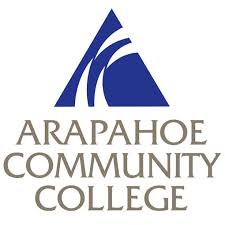
Three key elements can determine reliability in healthcare: effectiveness, timeliness, and patient focus. These processes must be capable of delivering the medication at the correct time and place without compromising patient health. These three factors are essential, but a reliable healthcare supply chain must also be tied to a patient-centric approach to integrated action.
Interconnectivity
Healthcare is one industry that could greatly benefit from greater interconnectivity. It can provide patients with fast, same-day delivery and on-demand access to needed medical services. The supply chain is a key component in making this vision a reality. Companies are addressing patient-centric needs by developing innovative solutions for direct-to-consumer delivery and flexible last-mile processes.
In order to combat emerging diseases and promote health, it is essential that we improve the delivery of health care. Many healthcare systems are striving to improve their processes and reduce costs. They also seek to build and foster integrated operations that bring together all the stakeholders. Recent years have seen a rapid increase in healthcare research. This has resulted in a self-sustaining discipline in operations.
Points of entry
There are several challenges that plague the supply chain of healthcare products. One such problem is misalignment of incentives. Healthcare faces rising costs and increased regulations. Healthcare organizations must have better visibility into the goods they purchase and ship to address these issues. This means that they must develop strategic partnerships to find ways to overcome these challenges.
A healthcare supply network is a group of interconnected relationships that can help deliver superior customer value at lower cost. This chain begins at the manufacturer of the medicine or healthcare supply and moves through distribution centers and hospitals. Hospitals can order medicine directly from the manufacturer or through distributors or group purchasing organizations. Distributors buy medicines in bulk and keep a large supply of medicines at their locations.
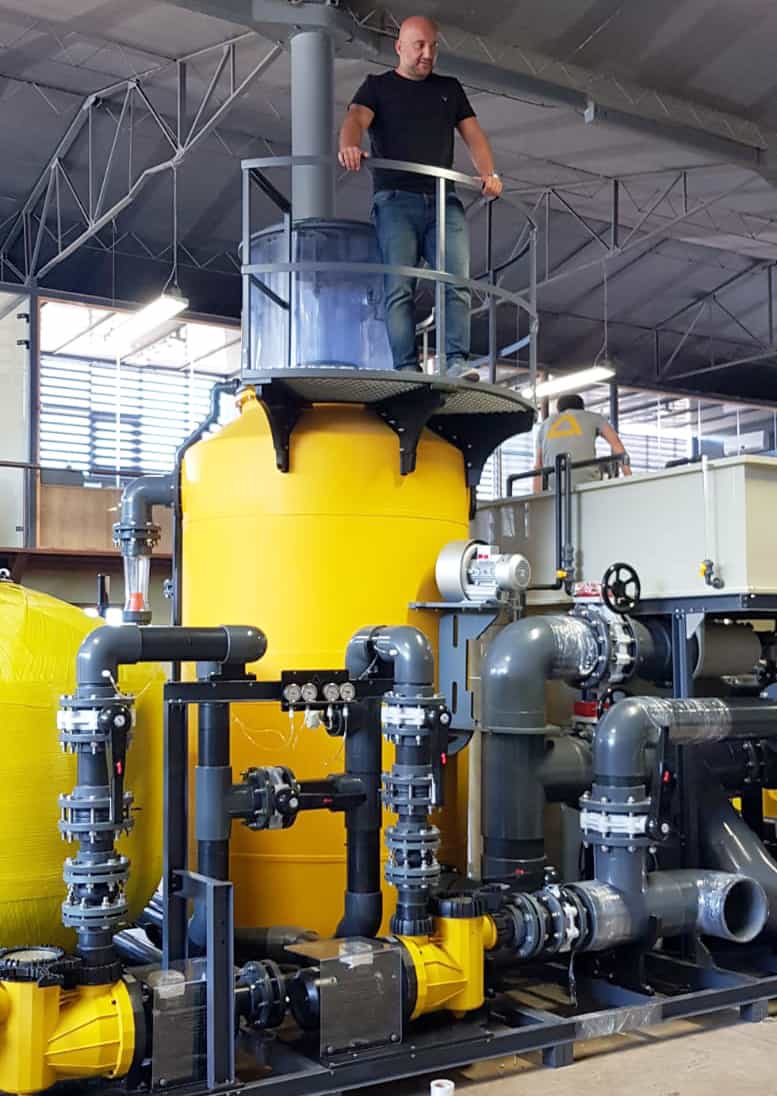
Human capital
Human capital is essential to the supply chain of healthcare. It manages the workforce, the quality of services, and the people who use it. This asset can be valuable if managed well. It can increase the success rate of businesses as well as maximize the worker's potential.
Human capital management consists of a variety of organizational strategies that are designed for building and maintaining employee engagement. Employee engagement is critical to the success of a company and can be measured using a variety if measures. Gallup reports that highly engaged business units experience 40% fewer quality incidents, achieve 10 percent higher customer metrics, and achieve 20% higher sales.
FAQ
What does Six Sigma mean?
Six Sigma employs statistical analysis to identify problems, measure them and analyze root causes. Six Sigma also uses experience to correct problems.
The first step in solving a problem is to identify it.
Next, data is collected and analyzed to identify trends and patterns.
The problem is then rectified.
Finally, data is reanalyzed to determine whether the problem has been eliminated.
This cycle will continue until the problem is solved.
Why does it sometimes seem so difficult to make good business decisions?
Businesses are complex systems, and they have many moving parts. Their leaders must manage multiple priorities, as well as dealing with uncertainty.
Understanding how these factors impact the whole system is key to making informed decisions.
You must first consider what each piece of the system does and why. Then, you need to think about how these pieces interact with one another.
It is also worth asking yourself if you have any unspoken assumptions about how you have been doing things. You might consider revisiting them if they are not.
For help, ask someone else if you're still stumped after all the above. You may be able to see things from a different perspective than you are and gain insight that can help you find a solution.
Why is it so important for companies that they use project management techniques
Project management techniques are used to ensure that projects run smoothly and meet deadlines.
This is because most businesses rely on project work for their products and services.
These projects must be managed efficiently and effectively by companies.
Companies can lose time, money, and reputation if they don't have a good project management system.
What are your main management skills
Business owners need to have management skills, no matter how small or large they may be. They include the ability to manage people, finances, resources, time, and space, as well as other factors.
These skills are necessary for setting goals and objectives as well as planning strategies, leading groups, motivating employees and solving problems.
As you can see there is no end to the number of managerial tasks.
How can we make our company culture successful?
A culture of respect and value within a company is key to a productive culture.
It's based on three main principles:
-
Everybody has something of value to share
-
People are treated fairly
-
It is possible to have mutual respect between groups and individuals
These values are reflected by the way people behave. They will treat others with consideration and courtesy.
They will respect the opinions of others.
They encourage others to express their feelings and ideas.
A company culture encourages collaboration and communication.
People are free to speak out without fear of reprisal.
They know that they will not be judged if they make mistakes, as long as the matter is dealt with honestly.
Finally, the company culture promotes honesty and integrity.
Everyone understands that the truth is always best.
Everyone is aware that rules and regulations apply to them.
People don't expect special treatment or favors.
What's the difference between Six Sigma and TQM?
The key difference between the two quality management tools is that while six-sigma focuses its efforts on eliminating defects, total quality management (TQM), focuses more on improving processes and reducing cost.
Six Sigma is an approach for continuous improvement. It emphasizes the elimination and improvement of defects using statistical methods, such as control charts, P-charts and Pareto analysis.
This method attempts to reduce variations in product output. This is done by identifying and correcting the root causes of problems.
Total Quality Management involves monitoring and measuring every aspect of the organization. It also includes training employees to improve performance.
It is often used to increase productivity.
Statistics
- Your choice in Step 5 may very likely be the same or similar to the alternative you placed at the top of your list at the end of Step 4. (umassd.edu)
- Hire the top business lawyers and save up to 60% on legal fees (upcounsel.com)
- The BLS says that financial services jobs like banking are expected to grow 4% by 2030, about as fast as the national average. (wgu.edu)
- UpCounsel accepts only the top 5 percent of lawyers on its site. (upcounsel.com)
- The average salary for financial advisors in 2021 is around $60,000 per year, with the top 10% of the profession making more than $111,000 per year. (wgu.edu)
External Links
How To
What is Lean Manufacturing?
Lean Manufacturing methods are used to reduce waste through structured processes. They were developed by Toyota Motor Corporation in Japan during the 1980s. It was designed to produce high-quality products at lower prices while maintaining their quality. Lean manufacturing is about eliminating redundant steps and activities from the manufacturing process. It has five components: continuous improvement and pull systems; just-in time; continuous change; and kaizen (continuous innovation). It is a system that produces only the product the customer requests without additional work. Continuous improvement means continuously improving on existing processes. Just-in-time refers to when components and materials are delivered directly to the point where they are needed. Kaizen is continuous improvement. This can be achieved by making small, incremental changes every day. Finally, 5S stands for sort, set in order, shine, standardize, and sustain. To achieve the best results, these five elements must be used together.
Lean Production System
Six key concepts form the foundation of the lean production system:
-
Flow - focuses on moving information and materials as close to customers as possible.
-
Value stream mapping - break down each stage of a process into discrete tasks and create a flowchart of the entire process;
-
Five S's - Sort, Set In Order, Shine, Standardize, and Sustain;
-
Kanban is a visual system that uses visual cues like stickers, colored tape or stickers to keep track and monitor inventory.
-
Theory of Constraints - Identify bottlenecks in the process, and eliminate them using lean tools such kanban boards.
-
Just-intime - Order components and materials at your location right on the spot.
-
Continuous improvement - Make incremental improvements rather than overhauling the entire process.