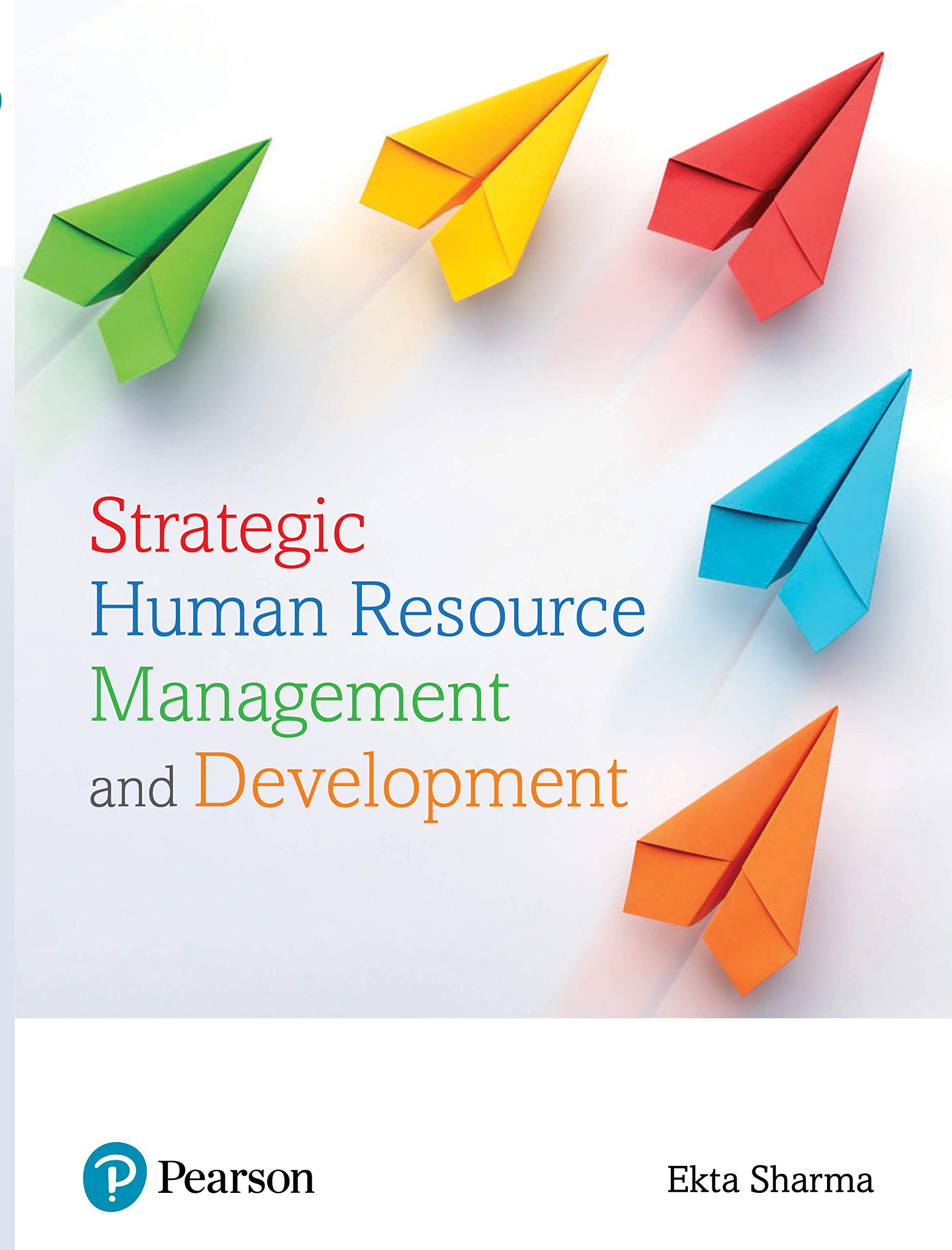
A business flow metric doesn't capture the inherent directionality or directionality supply networks. A supply network is often composed of many levels and dependencies. Additionally, a business flow measurement does not accurately capture the directionality of information flows within networks. Understanding and considering these issues is essential for the development of a digital supply network.
Sustainability
Multinational corporations need to ensure sustainability of their supply chains. Many companies have made sustainability their top priority and committed to using sustainable suppliers. However, many lower-level suppliers do not follow sustainability standards, posing serious risks for businesses. In order to combat this problem, the authors of this article looked at the supply networks of three MNCs and found several best practices that companies can adopt. These include setting longterm sustainability goals, and including lower-tier vendors in the sustainability plan.
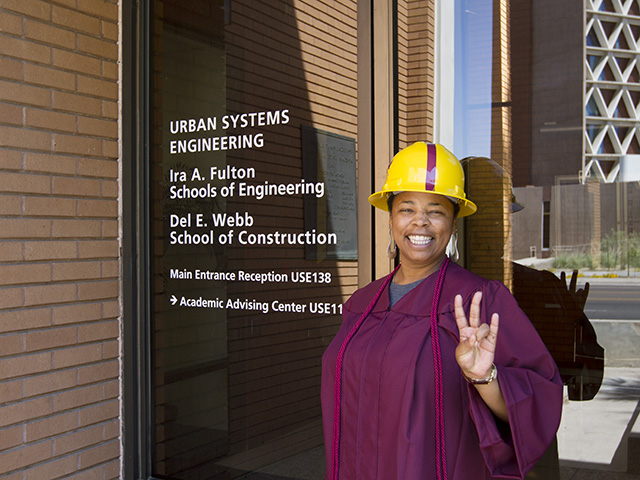
Companies must set targets and measure the progress they make in improving their supply chains. They must also involve all stakeholders in the supply chain, including internal staff who drive change and consumers. The goal should not be to prove the benefits to business of sustainable supply networks but to create the governance and organizational structures necessary to ensure that the sustainability efforts are a success.
Vertical disintegration
Vertical disintegration of supply chains can have a number of consequences for firms. This can result in higher costs and losses and may also cause changes to organisational structures and hierarchies. To improve their overall competitiveness, some companies might choose to decrease their involvement in upstream and downstream activities. However, this is not always a good idea and should only be done in exceptional circumstances.
Vertical integration has the disadvantage that it reduces flexibility. This is because it forces it to follow trends within a particular segment. It may prove difficult for retailers to adopt new technology if their competition already uses it. If that were true, the parent company would have the financial resources to purchase the new technology in order to keep pace with the competition. Integration can also be difficult due to the rapid evolution of technology. It can also be expensive for companies to integrate different technologies in different parts of their supply chain.
A digital supply network can have performance implications
There are many benefits to digital supply chains, such as increased efficiency, resilience, cost savings and cost savings. However, digital supply chains can increase cybersecurity risks. However, there are several approaches companies can use to mitigate these risks. Let's take a look at some of them. These methods involve the use of data analytics. With this technology, businesses can gain insight into customer expectations and improve their products and services. Companies can also use shared data from different sources to predict possible problems and make better, informed decisions.
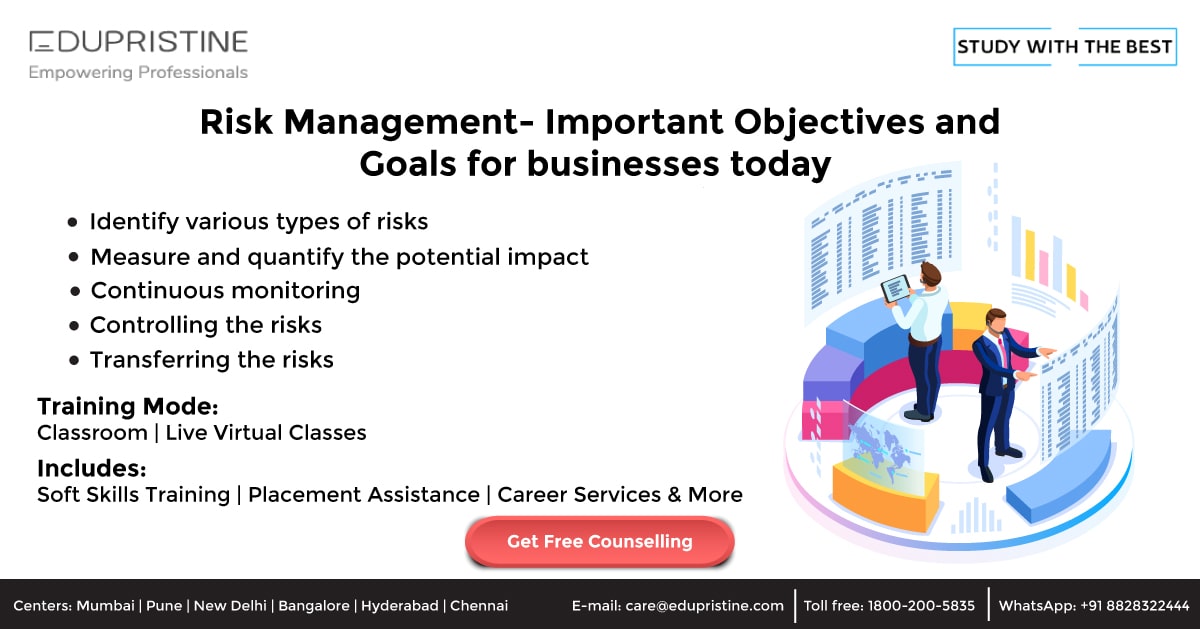
Assessing your supply chain is the first step towards digitalization. This will allow you to identify any issues and risks as well as potential complications. Then, you can develop an action plan to minimize any risks. Once you have a clear idea of the goals you want to achieve through the digital supply network, collaboration with your partners is essential. By working together, you can ensure the digital supply chain meets the needs of all parties.
FAQ
What do we mean when we say "project management"?
We mean managing the activities involved in carrying out a project.
Our services include the definition of the scope, identifying requirements, preparing a budget, organizing project teams, scheduling work, monitoring progress and evaluating the results before closing the project.
What are some common mistakes managers make when managing people?
Sometimes managers make it harder for their employees than is necessary.
They may not assign enough responsibilities to staff members and provide them with inadequate support.
In addition, many managers lack the communication skills required to motivate and lead their teams.
Managers set unrealistic expectations and make it difficult for their team.
Managers might try to solve every problem by themselves rather than delegating the responsibility.
How do we build a culture that is successful in our company?
A positive company culture creates a sense of belonging and respect in its people.
It's built on three fundamental principles:
-
Everybody can contribute something valuable
-
People are treated fairly
-
It is possible to have mutual respect between groups and individuals
These values reflect in how people behave. They will treat others with kindness and consideration.
They will respect other people's opinions.
They encourage others to express their feelings and ideas.
Additionally, the company culture encourages open communication as well as collaboration.
People feel safe to voice their opinions without fear of reprisal.
They know mistakes will be accepted as long as they are dealt with honestly.
Finally, the company culture promotes honesty and integrity.
Everyone knows that they must always tell truth.
Everyone recognizes that rules and regulations are important to follow.
No one is entitled to any special treatment or favors.
What are the five management processes?
These five stages are: planning, execution monitoring, review and evaluation.
Setting goals for the future requires planning. Planning includes setting goals for the future.
Execution takes place when you actually implement the plans. You need to make sure they're followed by everyone involved.
Monitoring is the process of evaluating your progress toward achieving your objectives. Monitoring should include regular reviews of performance against goals and budgets.
Reviews take place at the end of each year. They give you an opportunity to review the year and assess how it went. If not there are changes that can be made to improve the performance next year.
Evaluation takes place after the annual review. It helps to determine what worked and what didn’t. It also provides feedback on the performance of people.
How does Six Sigma work
Six Sigma employs statistical analysis to identify problems, measure them and analyze root causes. Six Sigma also uses experience to correct problems.
First, identify the problem.
Next, data are collected and analyzed in order to identify patterns and trends.
The problem can then be fixed by taking corrective measures.
Final analysis of data is done to determine if the problem has been solved.
This continues until the problem has been solved.
What is TQM?
The quality movement was born during the industrial revolution when manufacturing companies realized they could not compete on price alone. They needed to improve quality and efficiency if they were going to remain competitive.
Management realized the need to improve and created Total Quality Management, which focused on improving all aspects within an organization's performance. It included continuous improvement, employee involvement and customer satisfaction.
What is the difference in a project and program?
A project is temporary; a program is permanent.
A project is usually defined by a clear goal and a set deadline.
It is often carried out by a team of people who report back to someone else.
A program often has a set goals and objectives.
It is often implemented by one person.
Statistics
- Your choice in Step 5 may very likely be the same or similar to the alternative you placed at the top of your list at the end of Step 4. (umassd.edu)
- The BLS says that financial services jobs like banking are expected to grow 4% by 2030, about as fast as the national average. (wgu.edu)
- 100% of the courses are offered online, and no campus visits are required — a big time-saver for you. (online.uc.edu)
- The average salary for financial advisors in 2021 is around $60,000 per year, with the top 10% of the profession making more than $111,000 per year. (wgu.edu)
- Hire the top business lawyers and save up to 60% on legal fees (upcounsel.com)
External Links
How To
How do you get your Six Sigma license?
Six Sigma is an effective quality management tool that can improve processes and increase productivity. It is a process that helps businesses achieve consistent results in their operations. The name "Sigmas" comes from the Greek words "sigmas", meaning "six". Motorola was the first to develop this process. Motorola realized that standardizing manufacturing processes was necessary to make products more efficient and less expensive. The many people involved in manufacturing had caused problems with consistency. They used statistical tools such as Pareto analysis, control charts, and Pareto analysis to resolve the problem. Then, they would apply these techniques in every area of the operation. So, after applying this technique, they would be able to make changes where there was room for improvement. There are three main steps to follow when trying to get your Six Sigma certification. Find out if you are qualified. Before you take any exams, you'll need to take some classes. After you have passed the classes, you can start taking the exams. It is important to review everything that you have learned in class. Next, you'll be ready for the test. If you pass, your certification will be granted. Finally, your certifications will be added to your resume.