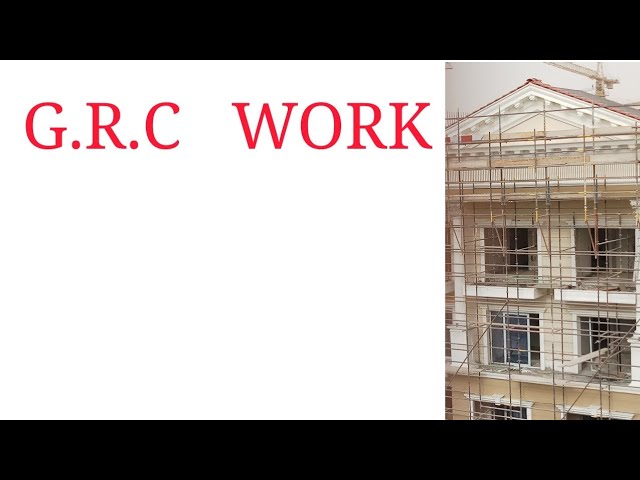
A ISO document has a number rules that are essential for understanding. The abbreviations should be clear and concise. Certain forms of punctuation should be avoided. These include symbols that represent quantities and certain forms of language. These guidelines help readers understand the ISO document's contents and make it easier to follow.
Forms
Implementing electronic ISO document forms can boost your company's quality processes, regulatory compliance, and customer satisfaction. Keep these forms simple and break them into data types. Make sure they are part a process. Agile development is important. It is important to get user requirements in advance. It's also important to test your software with users. You may discover problems that you hadn't anticipated. Additionally, all users should receive software-specific training.
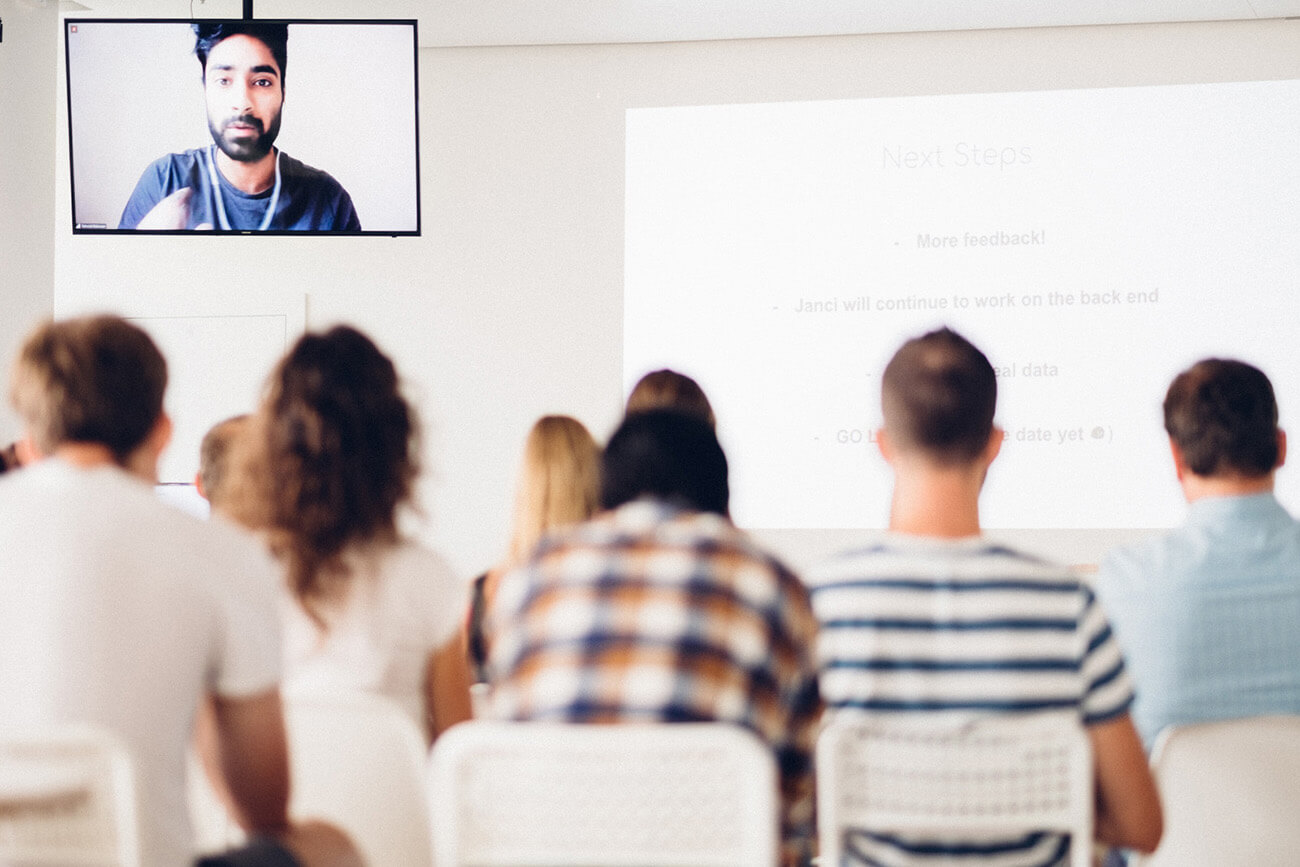
Symbols for quantities
The ISO documents use symbols to represent quantities. These symbols are commonly abbreviated terms. They are typically written in italics unlike numbers and words that are written in lowercase. Some abbreviations can also have special meanings. For example, 'net current value' or the 'internal rates of return'. The standard also specifies what symbols should be used when referring to quantities.
Acronyms
Most people are familiar with some common acronyms, especially if they read ISO documents regularly. CAR stands for Corrective Action Report. This acronym denotes an activity that causes a Corrective Act (CA). This is typically the investigation of a problem to identify its root cause, and prevent its recurrence. However, it can also be used to refer to the entire Corrective Action lifecycle.
Language
Language of ISO document plays a crucial role in ensuring that the document can be understood by its intended audience. Certain conventions characterize this language. Abbreviations are commonly used, but only the first word of a term is capitalized. The abbreviation for alternating current (ac) is acceptable, while radio frequency is not compatible with it.
Formatting
Documentation is an important aspect of ISO standards. Some organizations overdocument and create an inflexible system. Make sure your documentation adheres to the correct structure.
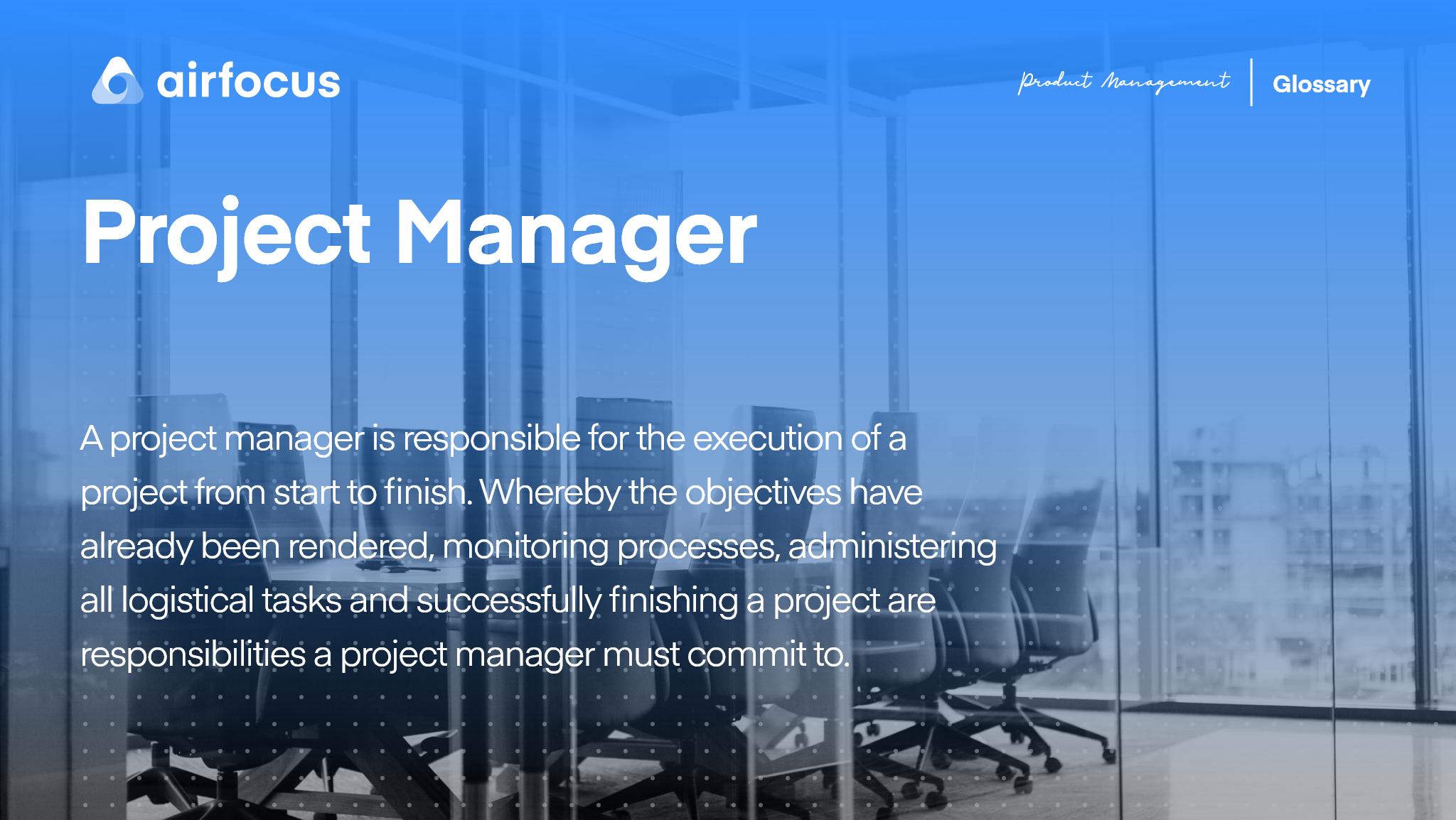
Publishing
ISO publishes documents in different formats. ISO documents are known as IEC standards and ISO standards. They are the product of the ISO/IEC JTC 1 and American Society for Testing and Materials. The ISO standards may not be the same as ASTM. Some standards may not be complete and therefore are not published. This is why their designation is often left out in the title of published works.
FAQ
Why is it so important for companies that they use project management techniques
Project management techniques are used to ensure that projects run smoothly and meet deadlines.
This is because most businesses rely heavily on project work to produce goods and services.
Companies need to manage these projects efficiently and effectively.
Companies could lose their time, reputation, and money without effective project management.
What are your main management skills
Management skills are essential for any business owner, whether they're running a small local store or an international corporation. These skills include the ability of managing people, finances, time, space, and other factors.
Managerial skills are required when setting goals and objectives and planning strategies, leading employees, motivating them, solving problems, creating policies, procedures, or managing change.
As you can see there is no end to the number of managerial tasks.
What are management concepts?
Management concepts are the fundamental principles and practices that managers use when managing people and their resources. These include topics such as human resource policies and job descriptions, performance assessments, training programs and employee motivation.
How to effectively manage employees
The key to effective management of employees is ensuring their happiness and productivity.
It is important to set clear expectations about their behavior and keep track of their performance.
Managers need clear goals to be able to accomplish this.
They need to communicate clearly with staff members. They need to communicate clearly with their staff.
They must also keep records of team activities. These include:
-
What was the result?
-
How much work was done?
-
Who did it, anyway?
-
How did it get done?
-
Why was it done?
This information is useful for monitoring performance and evaluating the results.
What is the best way to motivate your employees as a manager?
Motivation is the desire for success.
It is possible to be motivated by doing something you enjoy.
You can also feel motivated by making a positive contribution to the success in the organization.
If you are a doctor and want to be one, it will likely be more rewarding to see patients than to read medical books every day.
Another source of motivation is within.
One example is a strong sense that you are responsible for helping others.
Or you might enjoy working hard.
If you feel unmotivated, ask yourself why.
You can then think of ways to improve your motivation.
Why does it sometimes seem so hard to make good business decisions
Complex business systems have many moving parts. People who manage them have to balance multiple priorities while dealing with complexity and uncertainty.
The key to making good decisions is to understand how these factors affect the system as a whole.
You need to be clear about the roles and responsibilities of each system. You then need to consider how those individual pieces interact with each other.
Also, you should ask yourself if there have been any assumptions in your past behavior. If not, you might want to revisit them.
If you're still stuck after all this, try asking someone else for help. You may be able to see things from a different perspective than you are and gain insight that can help you find a solution.
Statistics
- The profession is expected to grow 7% by 2028, a bit faster than the national average. (wgu.edu)
- The BLS says that financial services jobs like banking are expected to grow 4% by 2030, about as fast as the national average. (wgu.edu)
- Hire the top business lawyers and save up to 60% on legal fees (upcounsel.com)
- 100% of the courses are offered online, and no campus visits are required — a big time-saver for you. (online.uc.edu)
- UpCounsel accepts only the top 5 percent of lawyers on its site. (upcounsel.com)
External Links
How To
How is Lean Manufacturing done?
Lean Manufacturing techniques are used to reduce waste while increasing efficiency by using structured methods. They were created in Japan by Toyota Motor Corporation during the 1980s. The goal was to produce quality products at lower cost. Lean manufacturing emphasizes removing unnecessary steps from the production process. It is made up of five elements: continuous improvement, continuous improvement, just in-time, continuous change, and 5S. It is a system that produces only the product the customer requests without additional work. Continuous improvement refers to continuously improving existing processes. Just-in-time refers to when components and materials are delivered directly to the point where they are needed. Kaizen means continuous improvement. Kaizen involves making small changes and improving continuously. Five-S stands for sort. It is also the acronym for shine, standardize (standardize), and sustain. These five elements are combined to give you the best possible results.
Lean Production System
Six key concepts are the basis of lean production:
-
Flow - focuses on moving information and materials as close to customers as possible.
-
Value stream mapping - break down each stage of a process into discrete tasks and create a flowchart of the entire process;
-
Five S’s - Sorted, In Order. Shine. Standardize. And Sustain.
-
Kanban – visual signals like colored tape, stickers or other visual cues are used to keep track inventory.
-
Theory of constraints - identify bottlenecks in the process and eliminate them using lean tools like kanban boards;
-
Just-in Time - Send components and material directly to the point-of-use;
-
Continuous improvement - incremental improvements are made to the process, not a complete overhaul.