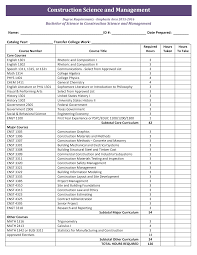
CSCMP stands as Certified Systems and Communications Manager and it is a valuable certification that can be used by communications and system professionals. CSCMP exam has 160 questions. It takes about four hours to complete. Pearson VUE, an independent company, administers the exam. Test centers are available worldwide. The test is proctored on the spot and confers pass/fail status.
Academic membership
Individuals in full-time academic positions in an accredited college or university can apply for academic membership in the CSCM. Annual dues are $175. This membership provides the opportunity to take part in collaborative forums and create course content. This membership gives members an opportunity to network and meet colleagues in their field. For more information on how to become a member, contact us.
Cost of membership
The Council of Supply Chain Management Professionals aims to connect, educate and develop supply chain professionals worldwide. For $149, you can join the group for six months and gain access to many of the organization's member events and benefits. Young professionals can also sign up for a six-month membership for only $88. Both membership options expire on August 31, 2021.
CSCMP members have access to all resources of the organization, including leading research and surveys. Members get first access to these research and actionable insights. Free webinars are offered by the organization. CSCMP membership allows you to learn more about supply chains management and improve your business operations.
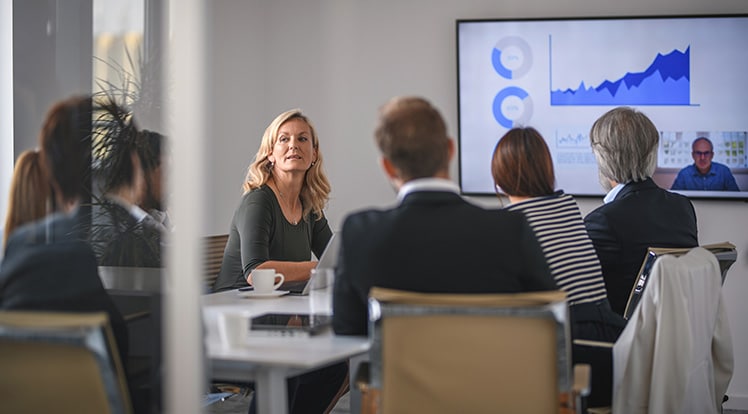
The SCMP level two exam is required to become a CSCMP membership. You can take the exam within one year of submitting your membership fee. A confirmation email will be sent to you approximately one week before your scheduled test date.
FAQ
What is Six Sigma and how can it help you?
It's a method for quality improvement that focuses on customer service as well as continuous learning. It is a method that eliminates defects using statistical techniques.
Motorola created Six Sigma as part of their efforts to improve manufacturing processes in 1986.
It was quickly adopted by the industry and many companies are now using six-sigma to improve product design, production, delivery, customer service, and product design.
What is a management tool to help with decision-making?
The decision matrix is a powerful tool that managers can use to help them make decisions. It allows them to consider all possible solutions.
A decision matrix represents alternatives in rows and columns. This allows one to see how each alternative impacts other options.
This example shows four options, each represented by the boxes on either side of the matrix. Each box represents one option. The top row displays the current situation, and the bottom row shows what might happen if nothing is done.
The effect of choosing Option 1 can be seen in column middle. It would translate into an increase in sales from $2million to $3million.
The following columns illustrate the impact of Options 2 and 3. These positive changes result in increased sales of $1 million and $500,000. They also have negative consequences. Option 2 increases costs by $100 thousand, while Option 3 decreases profits to $200 thousand.
The last column displays the results of selecting Option 4. This would result in a reduction of sales of $1 million.
A decision matrix has the advantage that you don’t have to remember where numbers belong. You can just glance at the cells and see immediately if one given choice is better.
This is because the matrix has already taken care of the hard work for you. Simply compare the numbers within the cells.
Here's an example of how you might use a decision matrix in your business.
You need to decide whether to invest in advertising. This will allow you to increase your revenue by $5000 per month. But, you will also incur additional expenses of $10 thousand per month.
You can calculate the net result of investing in advertising by looking at the cell directly below the one that says "Advertising." That number is $15 thousand. Advertising is worth more than its cost.
What are some common mistakes managers make?
Managers sometimes make their own job harder than necessary.
They may not be able to delegate enough responsibility to staff or provide adequate support.
In addition, many managers lack the communication skills required to motivate and lead their teams.
Some managers set unrealistic expectations for their staff.
Managers may prefer to solve every problem for themselves than to delegate responsibility.
What is Six Sigma?
Six Sigma uses statistics to measure problems, find root causes, fix them, and learn from past mistakes.
The first step is to identify the problem.
The next step is to collect data and analyze it in order to identify trends or patterns.
Then, corrective actions can be taken to resolve the problem.
Final analysis of data is done to determine if the problem has been solved.
This continues until you solve the problem.
What are the 3 main management styles?
These are the three most common management styles: participative (authoritarian), laissez-faire (leavez-faire), and authoritarian. Each style has its strengths and weaknesses. Which style do YOU prefer? Why?
Autoritarian – The leader sets the direction for everyone and expects them to follow. This style is most effective when an organization is large, stable, and well-run.
Laissez faire - Each individual can decide for himself/herself. This approach works best in small, dynamic organizations.
Participative – Leaders are open to suggestions and ideas from everyone. This style is best for small organizations where everyone feels valued.
What is the main difference between Six Sigma Six Sigma TQM and Six Sigma Six Sigma?
The key difference between the two quality management tools is that while six-sigma focuses its efforts on eliminating defects, total quality management (TQM), focuses more on improving processes and reducing cost.
Six Sigma can be described as a strategy for continuous improvement. It emphasizes the elimination of defects by using statistical methods such as control charts, p-charts, and Pareto analysis.
The goal of this method is to reduce variation in product output. This is achieved by identifying and addressing the root causes of problems.
Total Quality Management involves monitoring and measuring every aspect of the organization. It also involves training employees to improve performance.
It is commonly used as a strategy for increasing productivity.
Statistics
- The BLS says that financial services jobs like banking are expected to grow 4% by 2030, about as fast as the national average. (wgu.edu)
- As of 2020, personal bankers or tellers make an average of $32,620 per year, according to the BLS. (wgu.edu)
- Our program is 100% engineered for your success. (online.uc.edu)
- Hire the top business lawyers and save up to 60% on legal fees (upcounsel.com)
- Your choice in Step 5 may very likely be the same or similar to the alternative you placed at the top of your list at the end of Step 4. (umassd.edu)
External Links
How To
How can Lean Manufacturing be done?
Lean Manufacturing processes are used to reduce waste and improve efficiency through structured methods. They were developed by Toyota Motor Corporation in Japan during the 1980s. The primary goal was to make products with lower costs and maintain high quality. Lean manufacturing eliminates unnecessary steps and activities from a production process. It is composed of five fundamental elements: continuous improvement; pull systems, continuous improvements, just-in–time, kaizen, continuous change, and 5S. Pull systems involve producing only what the customer wants without any extra work. Continuous improvement is the continuous improvement of existing processes. Just-intime refers the time components and materials arrive at the exact place where they are needed. Kaizen stands for continuous improvement. Kaizen can be described as a process of making small improvements continuously. Five-S stands for sort. It is also the acronym for shine, standardize (standardize), and sustain. These five elements work together to produce the best results.
Lean Production System
Six key concepts are the basis of lean production:
-
Flow - focuses on moving information and materials as close to customers as possible.
-
Value stream mapping- This allows you to break down each step of a process and create a flowchart detailing the entire process.
-
Five S's – Sort, Put In Order Shine, Standardize and Sustain
-
Kanban - visual cues such as stickers or colored tape can be used to track inventory.
-
Theory of constraints: identify bottlenecks in your process and eliminate them using lean tools, such as kanban board.
-
Just-in Time - Send components and material directly to the point-of-use;
-
Continuous improvement is making incremental improvements to your process, rather than trying to overhaul it all at once.