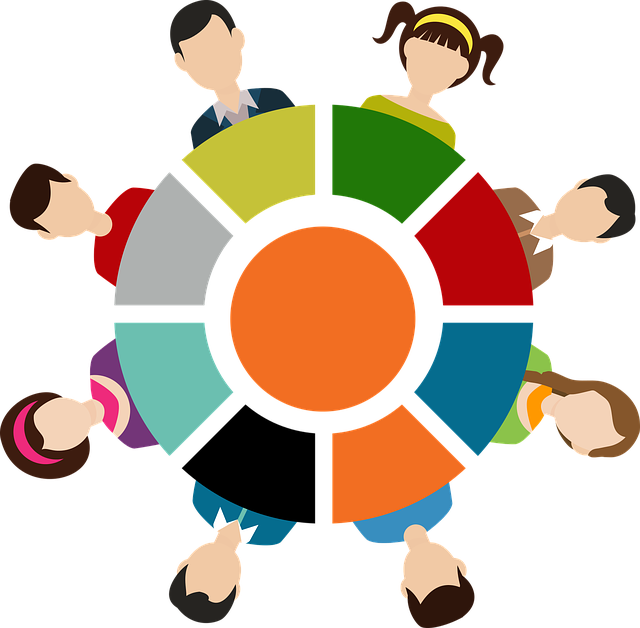
Project management best practices require the project manager to communicate well with all stakeholders and team members. This means empathizing with them and discussing all plans with them. It is helpful if the project manager has the right tools, such a project management program, that can streamline communication and record discussions.
Successful projects are built on communication.
Communication is essential for any project management initiative to succeed. It is crucial for the smooth flow information and tasks, and it helps to avoid many problems. It is useful for coordinating tasks and delegating them appropriately to groups. It is important that you understand the communication flow between upward and downward. Communication flows upward from upper-level managers to staff and downward from employees to upper-level managers.
Effective project management requires communication. It prevents confusion, builds trust among team members, and ensures that all stakeholders are aligned with project goals. Communication can be a key component of improving customer satisfaction. Businesses should encourage other stakeholders to voice their opinion on ongoing projects. You can use cloud call center software to give feedback, submit feedback via online surveys or any other forum.
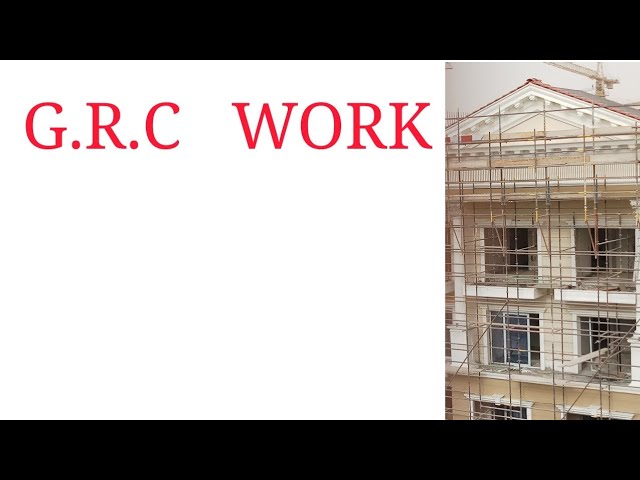
Before you begin a project, identify potential risks
One of the best methods for project management is to identify and manage risks before any project begins. You can do this by asking stakeholders for their input and making a list about the risks that are associated with your project. This list should include risks that relate to the project scope, cost, schedule, and people. You must also take into consideration any external risks.
It should be a topic of regular discussion in project meetings about risk identification. While some risks are obvious, others require more thorough analysis. Once identified, risks should be documented in an inventory, which can then be stored centrally. These tools are usually standardized and include risk categories, which identify areas most susceptible to certain risk events.
Establishing a risk management team
A risk response team is an important aspect of project management. This group should include experienced individuals who are familiar with the requirements of the project. They should have easy access to project plans and know about backup resources. They should be able to determine the worst-case scenario and devise a plan to deal with it.
Members of the project management team and external collaborators should make up the risk response teams. They should make action plans for each of the risk categories and determine how much extra time or resources they will need to respond to it. After identifying potential risks, the group should discuss the plan with all members of the team to get their approval.
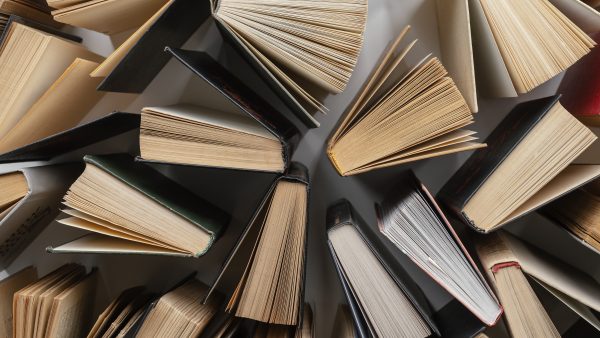
Setting up regular project meetings
Regular project meetings are an essential part of project management best practice. Meetings without clear objectives may drift off-track and disrupt schedules of other team members. This can negatively impact future attendance. Set SMART goals for meetings. These are Specific, Measurable. Achievable. Relevant. And Timely.
Meetings should be well-planned and involve all of the key stakeholders. The team should review the progress of the project at the beginning of every meeting and then ask for feedback from all stakeholders. It is also helpful to have a list of topics to be discussed before the meeting. This will help avoid having to guess which topics will be covered. Plan for contingencies by making adjustments to the agenda and schedule as required. Any changes should be handled in a disciplined manner, and any team members should be aware of any issues that might crop up during the meeting.
FAQ
What is the meaning of "project management?"
That is the management of all activities associated with a project.
We help you define the scope of your project, identify the requirements, prepare the budget, organize the team, plan the work, monitor progress and evaluate the results before closing down the project.
What is the difference between TQM and Six Sigma?
The main difference between these two quality management tools is that six sigma focuses on eliminating defects while total quality management (TQM) focuses on improving processes and reducing costs.
Six Sigma stands for continuous improvement. This method emphasizes eliminating defects using statistical methods such p-charts, control charts, and Pareto analysis.
This method aims to reduce variation in product production. This is accomplished through identifying and correcting root causes.
Total Quality Management involves monitoring and measuring every aspect of the organization. It also involves training employees to improve performance.
It is used to increase productivity.
What is the difference in a project and program?
A program is permanent, whereas a project is temporary.
A project is usually defined by a clear goal and a set deadline.
It is often performed by a team of people, who report back on someone else.
A program is usually defined by a set or goals.
It is usually implemented by a single person.
How do you effectively manage employees?
Managing employees effectively means ensuring that they are happy and productive.
It means setting clear expectations for them and keeping an eye on their performance.
Managers need clear goals to be able to accomplish this.
They need to communicate clearly and openly with staff members. They should also ensure that they both reward high performers and discipline those who are not performing to their standards.
They also need to keep records of their team's activities. These include:
-
What did you accomplish?
-
How much work was done?
-
Who did it, anyway?
-
What was the moment it was completed?
-
Why was this done?
This information can be used to monitor performance and evaluate results.
Statistics
- The BLS says that financial services jobs like banking are expected to grow 4% by 2030, about as fast as the national average. (wgu.edu)
- This field is expected to grow about 7% by 2028, a bit faster than the national average for job growth. (wgu.edu)
- As of 2020, personal bankers or tellers make an average of $32,620 per year, according to the BLS. (wgu.edu)
- Our program is 100% engineered for your success. (online.uc.edu)
- Your choice in Step 5 may very likely be the same or similar to the alternative you placed at the top of your list at the end of Step 4. (umassd.edu)
External Links
How To
How does Lean Manufacturing work?
Lean Manufacturing processes are used to reduce waste and improve efficiency through structured methods. They were developed in Japan by Toyota Motor Corporation (in the 1980s). The main goal was to produce products at lower costs while maintaining quality. Lean manufacturing focuses on eliminating unnecessary steps and activities from the production process. It consists of five basic elements: pull systems, continuous improvement, just-in-time, kaizen (continuous change), and 5S. Pull systems allow customers to get exactly what they want without having to do extra work. Continuous improvement is constantly improving upon existing processes. Just-intime refers the time components and materials arrive at the exact place where they are needed. Kaizen means continuous improvement. Kaizen involves making small changes and improving continuously. Finally, 5S stands for sort, set in order, shine, standardize, and sustain. These five elements are combined to give you the best possible results.
Lean Production System
Six key concepts are the basis of lean production:
-
Flow: The goal is to move material and information as close as possible from customers.
-
Value stream mapping: This is a way to break down each stage into separate tasks and create a flowchart for the entire process.
-
Five S’s - Sorted, In Order. Shine. Standardize. And Sustain.
-
Kanban: Use visual signals such stickers, colored tape, or any other visual cues, to keep track your inventory.
-
Theory of constraints: Identify bottlenecks and use lean tools such as kanban boards to eliminate them.
-
Just-intime - Order components and materials at your location right on the spot.
-
Continuous improvement - incremental improvements are made to the process, not a complete overhaul.