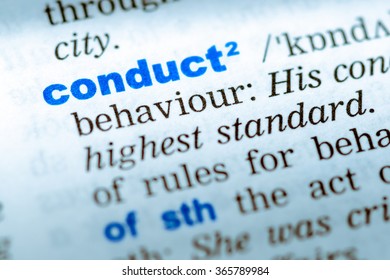
Supply chain success is based on five elements. These elements include working collaboratively with suppliers, reducing costs, and managing upstream and downstream business issues. Supply chain success requires that each of these elements be identified and implemented. Additionally, supply chain success is affected by government and regulatory agencies.
Five strategies to make supply chain success a reality
Supply chain management is essential to the success and satisfaction of any business, especially if your goal is to exceed customer expectations. This is why your supply chain strategy must focus on customer needs. This means that the fulfillment experience must live up to the brand's promises. If a brand promises quick delivery, it must be capable of fulfilling that promise. Customers are also attracted to the smallest details. They value thoughtfulness, which is a sign of the brand's thought process.
Supply chain success must address supplier issues. Delays can also be caused by suppliers having to pay tariffs. This can be overcome by sourcing alternative suppliers and bulk buying before tariffs are in place. These delays can be overcome by a supply chain solution. Software such as supply chain software can provide detailed information about inventory levels, inventory movement, and future needs.
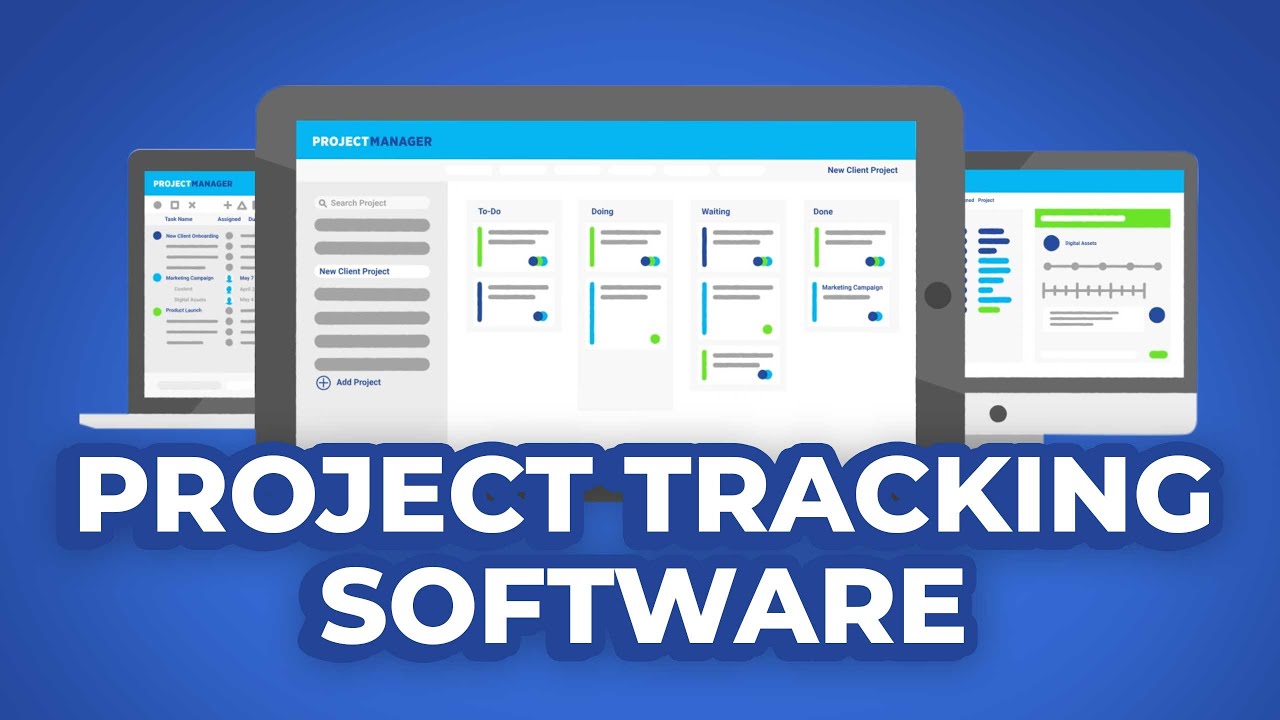
Governmental and regulatory bodies influence supply chain success
There are many factors that influence the success of supply chains, including regulations and government policies. The United States government spends federal funds to increase domestic capacity, develop markets abroad, and encourage collaboration between domestic companies and foreign countries. These mechanisms can be public, private, or cross-government. These efforts are made to assist companies in achieving their dual objectives. Companies rely on a trusted, robust global supply network.
This is particularly true for healthcare workers, since staff and patients' needs can have an impact on supply. For example, hospitals may need to keep stock of the right sizes of gloves, while some patients require customized medical products. Financial managers might want to reduce healthcare costs and out-of-date products, while others may prefer specific brands or types. It can cause disruption in supply chains if there is not enough coordination and alignment of incentives.
Collaboration with suppliers
Supply chain cooperation is the collaboration with suppliers to improve efficiency in a company’s procurement. It offers many benefits to both the supplier and the customer. Collaboration is more flexible than the traditional customer/supplier relationship and focuses more heavily on creating value. Collaboration allows companies to see their suppliers as strategic partners that they can work with to increase competitive advantage.
Collaboration between suppliers is crucial to the success and sustainability of a supply chain. Collaboration is only possible if both parties look for ways they can improve their relationship. This can be achieved by having regular meetings with all your suppliers. This will give you the opportunity to listen to their concerns and offer constructive feedback.
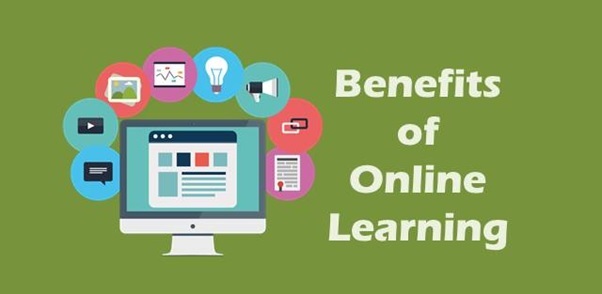
Managing upstream and downstream business issues
Supply chain management is the integration of many processes and tasks with an emphasis on delivering value for customers and other stakeholders. This can involve a range of issues including reputational, legal and operational risks. These issues can have an impact on the success or failure of a supply-chain. It is crucial to manage them.
The supply chain professionals need to be able to anticipate and address the major issues that impact their business. They also need to develop strong management plans. To address any potential problems, they need to create strong contracts and partner with suppliers and customers. Global economic instability and growing complexity are two factors that supply chain managers need to be proactive and vigilant in dealing with. In some cases, tariffs may be imposed on trade routes by political circumstances. This could lead to increased costs and longer processing times for customs, as well slowing down international shipping.
FAQ
What are some common mistakes managers make when managing people?
Managers can make their jobs more difficult than necessary.
They may not be able to delegate enough responsibility to staff or provide adequate support.
Managers often lack the communication skills necessary to motivate and guide their teams.
Some managers create unrealistic expectations for their teams.
Managers may prefer to solve every problem for themselves than to delegate responsibility.
What are the four major functions of Management?
Management is responsible for organizing, managing, directing and controlling people, resources, and other activities. It also includes developing policies and procedures and setting goals.
Organizations can achieve their goals through management. This includes leadership, coordination, control and motivation.
The four main functions of management are:
Planning - Planning is about determining what must be done.
Organizing - Organizing involves deciding how things should be done.
Directing - This refers to getting people follow instructions.
Controlling – This refers to ensuring that tasks are carried out according to plan.
What kind people use Six Sigma?
Six Sigma is well-known to those who have worked in operations research and statistics. Anybody involved in any aspect or business can benefit.
Because it requires a high level of commitment, only those with strong leadership skills will make an effort necessary to implement it successfully.
Six Sigma is so popular.
Six Sigma is easy to use and can lead to significant improvements. Six Sigma provides a framework to measure improvements and allows companies to focus on the most important things.
Statistics
- Hire the top business lawyers and save up to 60% on legal fees (upcounsel.com)
- UpCounsel accepts only the top 5 percent of lawyers on its site. (upcounsel.com)
- The BLS says that financial services jobs like banking are expected to grow 4% by 2030, about as fast as the national average. (wgu.edu)
- This field is expected to grow about 7% by 2028, a bit faster than the national average for job growth. (wgu.edu)
- The profession is expected to grow 7% by 2028, a bit faster than the national average. (wgu.edu)
External Links
How To
How can Lean Manufacturing be done?
Lean Manufacturing is a method to reduce waste and increase efficiency using structured methods. These processes were created by Toyota Motor Corporation, Japan in the 1980s. The goal was to produce quality products at lower cost. Lean manufacturing is about eliminating redundant steps and activities from the manufacturing process. It is composed of five fundamental elements: continuous improvement; pull systems, continuous improvements, just-in–time, kaizen, continuous change, and 5S. Pull systems are able to produce exactly what the customer requires without extra work. Continuous improvement involves constantly improving upon existing processes. Just-in-time is when components and other materials are delivered at their destination in a timely manner. Kaizen means continuous improvement, which is achieved by implementing small changes continuously. Finally, 5S stands for sort, set in order, shine, standardize, and sustain. To achieve the best results, these five elements must be used together.
Lean Production System
Six key concepts underlie the lean production system.
-
Flow - The focus is on moving information and material as close as possible to customers.
-
Value stream mapping is the ability to divide a process into smaller tasks, and then create a flowchart that shows the entire process.
-
Five S's: Sort, Shine Standardize, Sustain, Set In Order, Shine and Shine
-
Kanban is a visual system that uses visual cues like stickers, colored tape or stickers to keep track and monitor inventory.
-
Theory of constraints - identify bottlenecks during the process and eliminate them with lean tools like Kanban boards.
-
Just-in time - Get components and materials delivered right at the point of usage;
-
Continuous improvement - Make incremental improvements rather than overhauling the entire process.