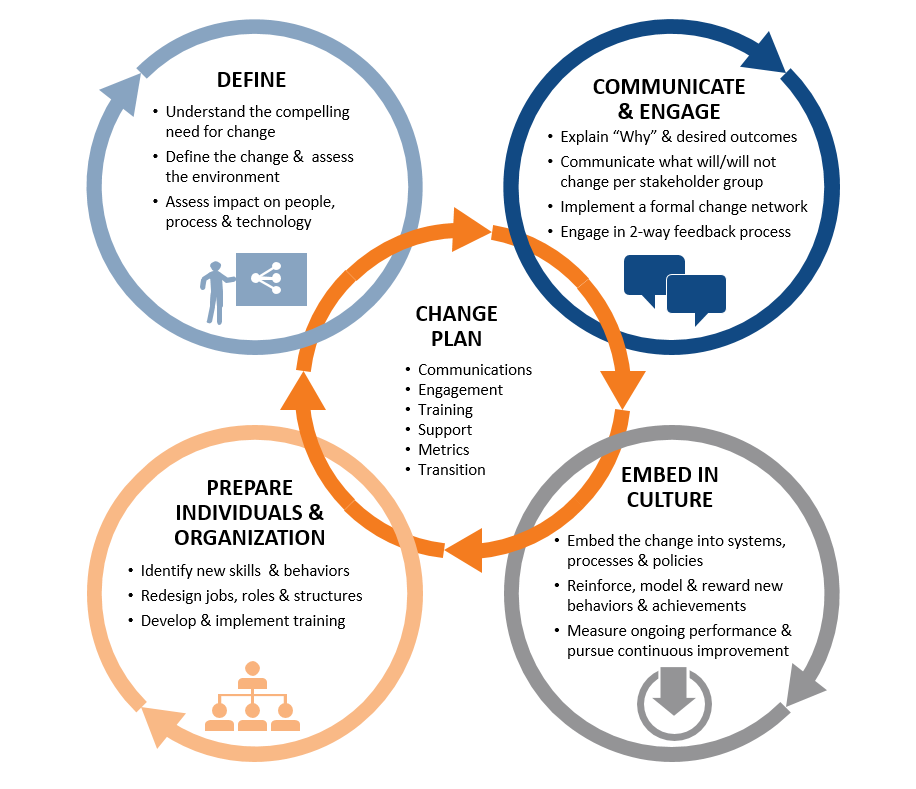
Planning is a collection of management activities that involves formulating goals objectives and actions. It is concerned with what needs to be done and how to do it. It is the process of defining the goals and means for a project or activity. It is the process that identifies a course, determines resources, and decides how to get there. A good plan is a key component to any project or organization's success. Here are some suggestions for planning.
Plan
Simply put, planning is the process by which an organization determines its goals. It is an essential tool for decision making as it determines when and what actions to take to achieve these goals. There are many kinds of plans. What type of organization you have will determine which plan is best for you. Some plans are specific and detailed, while others have more flexibility and can be altered over time.
Planning is the art of anticipating what the future will bring and then deciding the best course. It involves thinking ahead and analysing data before deciding on the best course of action. This process involves defining the objectives of a project or business and correlating them to opportunities in the business world. Planning is an integral function that involves problem solving. It is the first managerial function within the management process. Here are some examples of how planning can help an organization reach its goals:
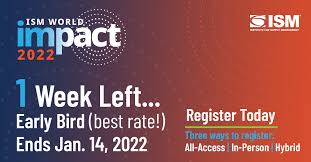
Organize
Organizational planning helps companies to achieve their goals and respond quickly to changes in the workplace. It helps clarify roles and responsibilities as well as expectations. It helps companies react to workplace changes and achieve greater success than if they did not have it. You can get started by using an organizational planning software program. These are the most important features of an organizational plan software program. These features make your work much easier and more effective. You will learn more about how organizational planning is a key to ensuring your company's success.
Planning requires organizing. It involves determining the situation, making decisions and then taking action. The process of organizing involves setting priorities and devising complex plans to achieve a goal. It is also an important part of management and will ensure the effectiveness and efficiency of an organization. Once a plan has been created, the next step is organizing it so that it will be as effective and efficient as possible. Ultimately, organizing will help your organization achieve its goals by delivering its mandate.
Decide on course of action
Plan is the process by which you choose a future course. Planning involves considering various options and deciding which one is best. To ensure the success of an organization, a plan should be as precise as possible. This is an essential aspect of project management. These are three ways to decide which course of action is best. Identify your goals and objectives and then create a detailed plan. Once you've created a plan, you'll be able to implement it properly.
Find resources
Project planning begins with determining the resources. It is essential to know the available resources and how you plan to use them in order for a project to be successful. To determine the resources needed, you must first identify the tasks to be completed. This can be done on a Gantt chart or task list, with estimated start and end dates. Next, you will need to decide which resources are required to complete these tasks. Next, enter these information into your planning program.
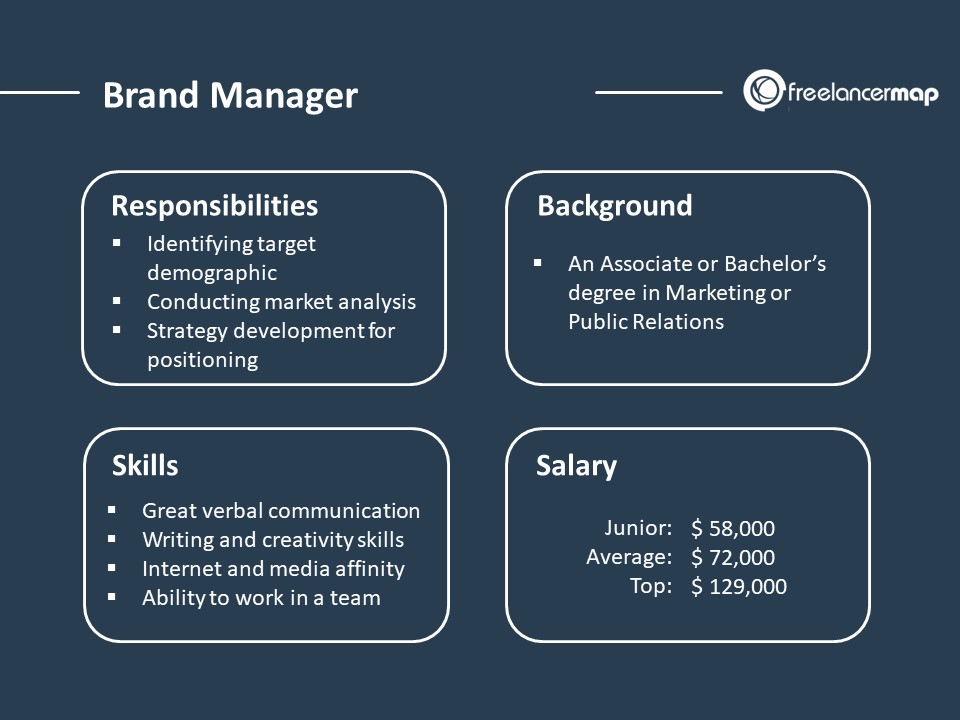
Resource planning is a necessary part of planning, because if you don't know what kind of resources you'll need, your project will suffer. A project task list can help you determine how many resources you will need. This can make hiring easier. Additionally, this type of planning can help you keep track of the time and resources needed for each task. For instance, a large project may require several team members working overtime to complete all the tasks.
FAQ
How do we build a culture that is successful in our company?
A positive company culture creates a sense of belonging and respect in its people.
It is based on three principles:
-
Everybody has something of value to share
-
People are treated fairly
-
It is possible to have mutual respect between groups and individuals
These values are reflected in the way people behave. They will treat others with consideration and courtesy.
They will respect other people's opinions.
These people will inspire others to share thoughts and feelings.
Company culture also encourages open communication, collaboration, and cooperation.
People can freely express their opinions without fear or reprisal.
They understand that errors will be tolerated as long they are corrected honestly.
Finally, the company culture encourages honesty as well as integrity.
Everybody knows they have to tell the truth.
Everyone is aware that rules and regulations apply to them.
And no one expects special treatment or favors.
How does a manager develop his/her management skills?
It is important to have good management skills.
Managers should monitor the performance and progress of their subordinates.
You should immediately take action if you see that your subordinate is not performing as well as you would like.
You should be able pinpoint what needs to improve and how to fix it.
Six Sigma is so popular.
Six Sigma can be implemented quickly and produce impressive results. It can also be used to help companies identify and focus on the most important aspects of their business.
What is Six Sigma, exactly?
It's a method for quality improvement that focuses on customer service as well as continuous learning. It is a method that eliminates defects using statistical techniques.
Six Sigma was developed at Motorola in 1986 as part of its efforts to improve manufacturing processes.
The idea spread quickly in the industry. Today many organizations use six-sigma techniques to improve product design.
Statistics
- Hire the top business lawyers and save up to 60% on legal fees (upcounsel.com)
- UpCounsel accepts only the top 5 percent of lawyers on its site. (upcounsel.com)
- The BLS says that financial services jobs like banking are expected to grow 4% by 2030, about as fast as the national average. (wgu.edu)
- This field is expected to grow about 7% by 2028, a bit faster than the national average for job growth. (wgu.edu)
- As of 2020, personal bankers or tellers make an average of $32,620 per year, according to the BLS. (wgu.edu)
External Links
How To
How do you do the Kaizen method?
Kaizen means continuous improvement. The Japanese philosophy emphasizes small, incremental improvements to achieve continuous improvement. This term was created by Toyota Motor Corporation in 1950. This is a collaborative process in which people work together to improve their processes continually.
Kaizen is one of the most effective methods used in Lean Manufacturing. This concept requires employees to identify and solve problems during manufacturing before they become major issues. This will increase the quality and decrease the cost of the products.
Kaizen is the idea that every worker should be aware of what is going on around them. So that there is no problem, you should immediately correct it if something goes wrong. So, if someone notices a problem while working, he/she should report it to his/her manager.
There are some basic principles that we follow when doing kaizen. The end product is always our starting point and we work toward the beginning. We can improve the factory by first fixing the machines that make it. First, we fix machines that produce components. Next, we fix machines that produce raw material. And finally, we fix the workers who work directly with those machines.
This method is known as kaizen because it focuses upon improving every aspect of the process step by step. When we are done fixing the whole factory, we go back to the beginning and continue until we reach perfection.
It is important to understand how to measure the effectiveness and implementation of kaizen in your company. There are many methods to assess if kaizen works well. Another way to determine if kaizen is working well is to look at the quality of the products. Another way is to check how much productivity has grown since kaizen was implemented.
A good way to determine whether kaizen has been implemented is to ask why. Is it because the law required it or because you want to save money. Did you really believe it would lead to success?
Let's say you answered yes or all of these questions. Congratulations! You are ready to start kaizen.