
A safe management system is a collection of safes located in a retail area. Each safe includes a small amount software. Each terminal unit's processing capacity and memory is limited to well-defined functions. The central server manages key control parameters. It can be a network server or a cloud server. The safes themselves do not usually have an internet connection. This means that external hardware is not necessary.
Safe management system collects data
Safety management systems are a system that combines processes and procedures to reduce the risk of safety incidents. These systems can be highly effective but cannot eliminate all possible errors because they would not be practical, feasible, workable, or cost-effective. A safety management system cannot measure the behavior of every worker, so the information collected by it is not completely reliable. This information is nevertheless important for ensuring safety in the workplace.
To improve safety performance, managers must have access to data from the system and analyze it. These data can often be used by statistical techniques or other data sources. However, the information must be meaningfully presented. Additionally, reports should identify trends that managers can use to allocate resources more effectively. Safety management systems must adapt to these trends and should make it easy for managers to interpret the data and take action.
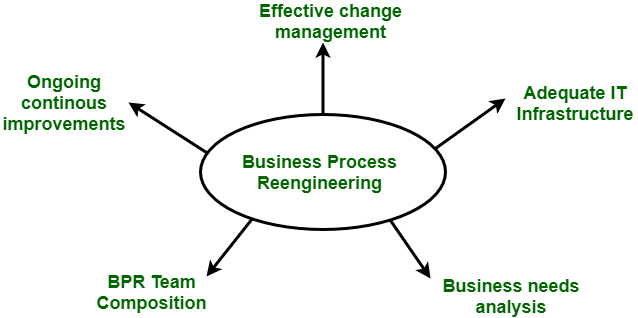
Documentation
The key ingredient to creating a safe management process is documentation. This helps to avoid making mistakes and prevents you from having to re-learn old lessons. A management system should normally include processes that handle miscellaneous information, process safety management, labeling and record keeping. Documentation serves to prevent injuries and illnesses, as well as help avoid accidents. Stakeholders have easy access to a complete document that outlines the best practices.
Good SMS documentation systems must contain all relevant national and international regulations and processes. The documentation should describe the outputs and organization of the safety management system. Documentation should also contain clear guidelines for keeping records. Safety documentation must be approved by the oversight authorities in order to be effective. You must also make sure that it reflects the latest changes made.
Risk matrix
A risk matrix is a tool that can help you manage your organization's risks. Using a risk matrix helps you prioritize the risks based on their impact. The risk matrix calculates the risk level by using categories such as Impact and Probability. Once you have established the risks to your business, you can use your risk matrix to strengthen your safety culture and improve your risk control. Here are some suggestions to help you make a risk matrix.
First, create a risk matrix. This document shows three types of risk. Each level represents a different type of risk. In Figure A1, you can see that the ground floor is the quantitative relationship between severity (probability) and the probability of the next level. The middle floor shows linear scaling. The top floor is carpeted. Each column is a risk indicator, and each value is represented numerically. Each cell contains a risk indicator. This is determined using the following formula: RixCj.
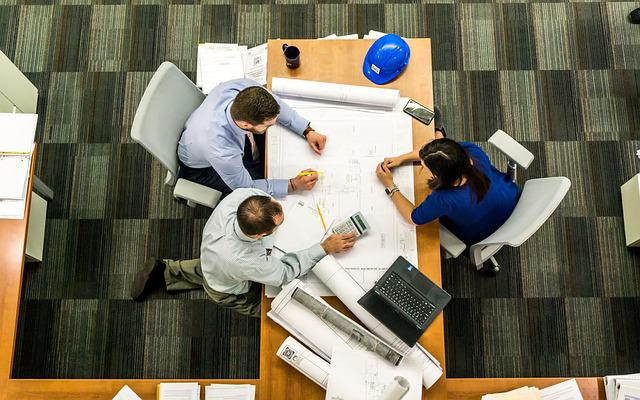
Security assurance
When developing a safety management plan, it is important that you define the requirements for a safety procedure. Safety assurance procedures should contain all resources, reporting requirements and disciplinary actions. The procedure should also include a documented safety plan that is shared with all employees and regularly reviewed. The safety policy should include a list of the different levels within an organization that are able to make decisions regarding safety. The certificate holder should also indicate the types and levels of personnel and resources responsible for maintaining safety management.
In response to growing industrial exploitation, the concept of safety assurance was created. The industrial revolution created significant commercial opportunities for Western societies. Business owners were driven to use a low-skilled workforce including child labour and rural migrants to meet their financial obligations. Under these conditions, injuries, death, and accidents were all too common. Safety management has emerged as an alternative to the exploitation of labour.
FAQ
Why is it important that companies use project management methods?
Project management techniques are used in order to ensure projects run smoothly, and that deadlines are met.
This is due to the fact that most businesses rely heavily upon project work in order to produce goods, and services.
These projects are essential for companies.
Without effective project management, companies may lose money, time, and reputation.
What is the difference between project and program?
A program is permanent while a project can be temporary.
Projects usually have a goal and a deadline.
It is often done in a team that reports to another.
A program often has a set goals and objectives.
It is usually implemented by a single person.
How do you manage your employees effectively?
The key to effective management of employees is ensuring their happiness and productivity.
It is important to set clear expectations about their behavior and keep track of their performance.
Managers need clear goals to be able to accomplish this.
They should communicate clearly to staff members. And they need to ensure that they reward good performance and discipline poor performers.
They will also need to keep records about their team's activities. These include:
-
What was accomplished?
-
How much work did you put in?
-
Who did it and why?
-
It was done!
-
Why it was done?
This information can help you monitor your performance and to evaluate your results.
What is TQM?
The industrial revolution led to the birth and growth of the quality movement. Manufacturing companies realized they couldn't compete solely on price. They needed to improve quality and efficiency if they were going to remain competitive.
In response to this need for improvement, management developed Total Quality Management (TQM), which focused on improving all aspects of an organization's performance. It included continuous improvement, employee involvement and customer satisfaction.
Six Sigma is so popular.
Six Sigma can be implemented quickly and produce impressive results. It also provides a framework for measuring improvements and helps companies focus on what matters most.
What kind of people use Six Sigma?
People who have worked with statistics and operations research will usually be familiar with the concepts behind six sigma. Anybody involved in any aspect or business can benefit.
Because it requires a high level of commitment, only those with strong leadership skills will make an effort necessary to implement it successfully.
What is Six Sigma?
This is a method of quality improvement that emphasizes customer service, continuous learning, and customer service. The goal is to eliminate defects by using statistical techniques.
Motorola's 1986 efforts to improve manufacturing process efficiency led to the creation of Six Sigma.
This idea quickly spread throughout the industry. Today, many organizations use six sigma methods for product design, production and delivery.
Statistics
- UpCounsel accepts only the top 5 percent of lawyers on its site. (upcounsel.com)
- The BLS says that financial services jobs like banking are expected to grow 4% by 2030, about as fast as the national average. (wgu.edu)
- Your choice in Step 5 may very likely be the same or similar to the alternative you placed at the top of your list at the end of Step 4. (umassd.edu)
- Hire the top business lawyers and save up to 60% on legal fees (upcounsel.com)
- 100% of the courses are offered online, and no campus visits are required — a big time-saver for you. (online.uc.edu)
External Links
How To
How can you implement the Kaizen technique?
Kaizen means continuous improvement. Kaizen is a Japanese concept that encourages constant improvement by small incremental changes. It's a process where people work together to improve their processes continuously.
Kaizen, a Lean Manufacturing method, is one of its most powerful. This concept requires employees to identify and solve problems during manufacturing before they become major issues. This is how you can improve the quality and lower the cost.
Kaizen is about making everyone aware of the world around them. If something is wrong, it should be corrected immediately so that no problem occurs. It is important that employees report any problems they see while on the job to their managers.
Kaizen has a set of basic principles that we all follow. The end product is always our starting point and we work toward the beginning. For example, if we want to improve our factory, we first fix the machines that produce the final product. We then fix the machines producing components, and the machines producing raw materials. Finally, we repair the workers who are directly involved with these machines.
This is why it's called "kaizen" because it works step-by-step to improve everything. We finish fixing the factory and then go back to the beginning. This continues until we achieve perfection.
How to measure kaizen's effectiveness in your business is essential to implement it. There are many ways to tell if kaizen is effective. Another method is to see how many defects are found on the products. Another way is to check how much productivity has grown since kaizen was implemented.
A good way to determine whether kaizen has been implemented is to ask why. You were trying to save money or obey the law? Did you really believe it would lead to success?
If you answered yes to any one of these questions, congratulations! You are now ready to begin kaizen.