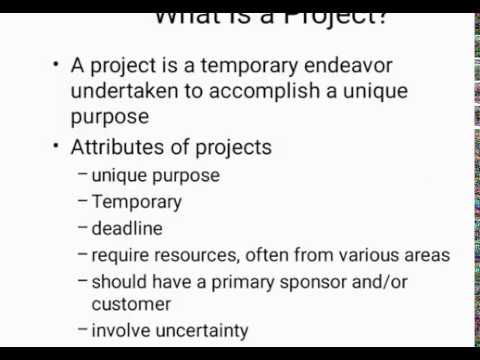
No matter which industry an organization works in, there is always risk. There is always risk, regardless of whether it is the industry or the business itself. It's possible to minimize the risk by identifying the risk and implementing the controls.
Every organization should be aware of the importance of inherent risk. It is a measure of the potential risk to a particular operation or process before any controls are put in place. The complexity of the activities involved can increase the risk. It does not have to be there. Although the risk level can be lower in some cases, it still poses a significant risk.
The degree of inherent risk an organization is exposed to is also an indicator. A weak IT infrastructure will lead to higher inherent risks. Because of this, the organization's infrastructure is more vulnerable to attacks. Organizations should have formal plans for monitoring their security status. It is important to include cybersecurity controls in those plans.
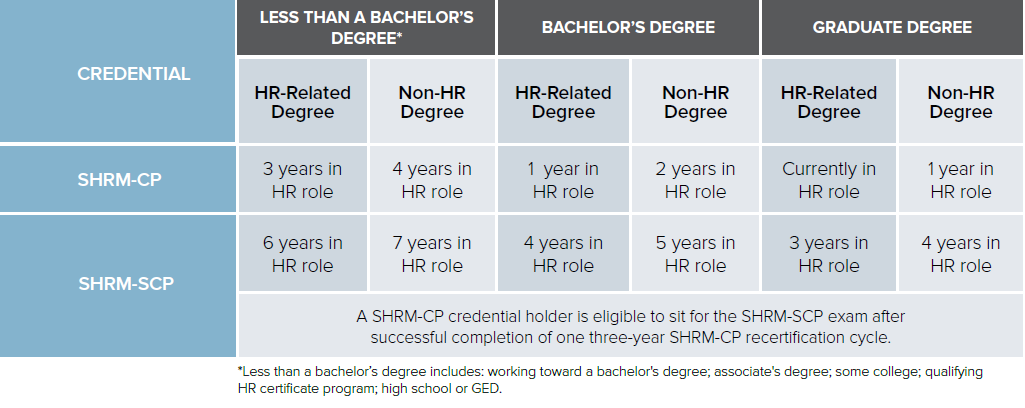
An example of inherent risk would be a company that does not have antivirus software installed on its computer system. There is a possibility that data could be stolen if malware is installed on the computer by an attacker. The chances of internal information theft are reduced if there is a robust logging and monitoring system.
FFIEC developed an assessment procedure to assist financial institutions with assessing their risk. This protocol provides a framework which allows for the measurement of the value-at-risk (VaR), within a given process. This protocol can be used to help identify risks before they could cause harm. This is a very simple process and it may not be as accurate.
It is crucial to distinguish between inherent and persistent risks. These are two different concepts. It is possible for an organization to have a strong IT system, but still face residual risks. This is because organizations will have to continuously re-evaluate their risk tolerance. It is best to use a systematic approach to risk assessment.
Residual Risk is any risk that persists despite all efforts by an organization or its security team. An evaluation of residual risks will help to identify potential vulnerabilities that cybercriminals may exploit before they happen. The residual risk assessment will also assess the impact of security controls on an exposure. FFIEC recommends an organization use a strong set of controls in order to minimize residual risk.
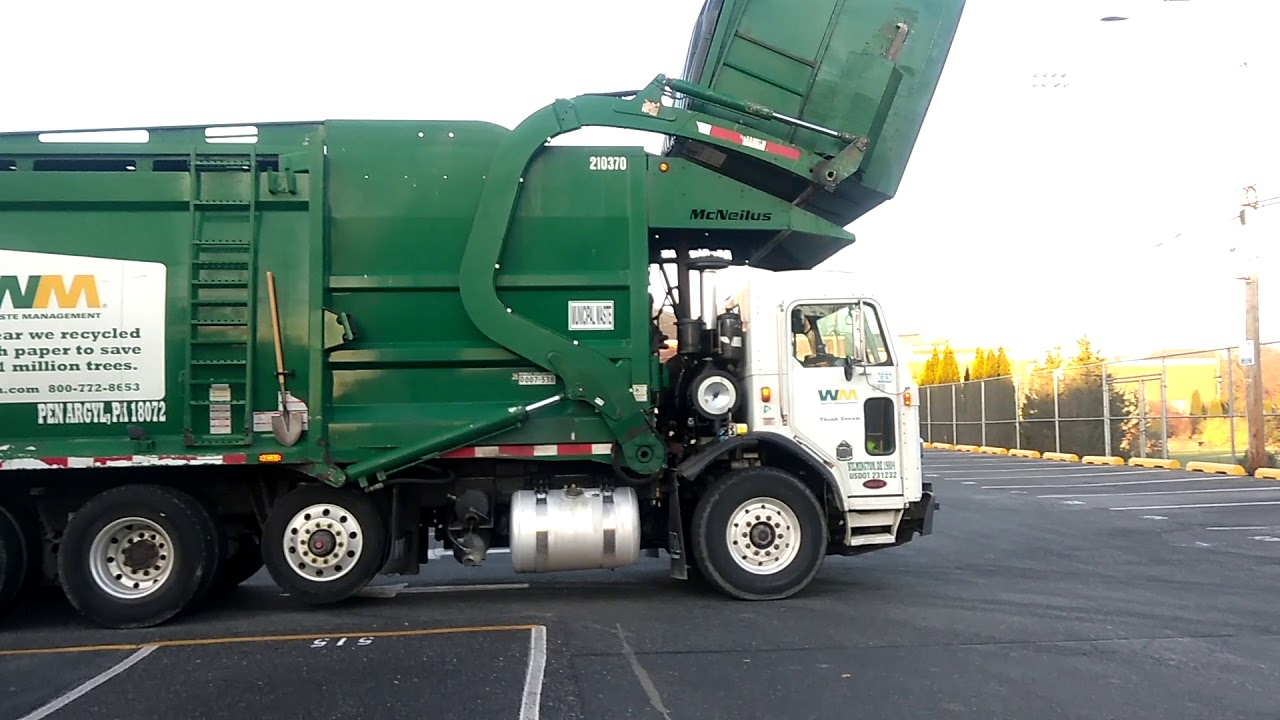
However, residual risk does not have to be evaluated without considering the value of inherent risk. Even though residual risk is usually measured before control measures are put in place, it can also measured after the controls have been implemented. This can be used to measure the effectiveness and efficiency of the controls.
FAQ
What is TQM, exactly?
The quality movement was born during the industrial revolution when manufacturing companies realized they could not compete on price alone. They had to improve efficiency and quality if they were to remain competitive.
Management responded to the need to improve, and developed Total Quality Management (TQM). This focused on improving every aspect of an organization’s performance. It included continuous improvement, employee involvement and customer satisfaction.
What is the difference between Six Sigma Six Sigma and TQM?
The major difference between the two tools for quality management is that six Sigma focuses on eliminating defect while total quality control (TQM), on improving processes and decreasing costs.
Six Sigma is a methodology for continuous improvement. This method emphasizes eliminating defects using statistical methods such p-charts, control charts, and Pareto analysis.
This method has the goal to reduce variation of product output. This is accomplished by identifying the root cause of problems and fixing them.
Total quality management is the measurement and monitoring of all aspects within an organization. Training employees is also part of total quality management.
It is commonly used as a strategy for increasing productivity.
What are the 3 main management styles?
The three major management styles are authoritarian (left-faire), participative and laissez -faire. Each style has its advantages and disadvantages. Which style do yo prefer? Why?
Autoritarian – The leader sets the direction for everyone and expects them to follow. This style works best if the organization is large and stable.
Laissez-faire – The leader gives each individual the freedom to make decisions for themselves. This style is best when the organization has a small but dynamic group.
Participative: The leader listens to everyone's ideas and suggestions. This is a great style for smaller organizations that value everyone.
How can a manager motivate employees?
Motivation is the desire to do well.
Enjoyable activities can motivate you.
You can also be motivated by the idea of making a difference to the success and growth of your organization.
If you are a doctor and want to be one, it will likely be more rewarding to see patients than to read medical books every day.
Motivation comes from within.
You may feel strongly that you are responsible to help others.
You might even enjoy the work.
If you don't feel motivated, ask yourself why.
Then, consider ways you could improve your motivation.
What does Six Sigma mean?
Six Sigma employs statistical analysis to identify problems, measure them and analyze root causes. Six Sigma also uses experience to correct problems.
The first step in solving a problem is to identify it.
The data is then analyzed and collected to identify trends.
Then corrective actions are taken to solve the problem.
The data are then reanalyzed to see if the problem is solved.
This cycle will continue until the problem is solved.
What does "project management" mean?
Management is the act of managing activities in order to complete a project.
Our services include the definition of the scope, identifying requirements, preparing a budget, organizing project teams, scheduling work, monitoring progress and evaluating the results before closing the project.
What is the difference of a program and project?
A project is temporary; a program is permanent.
A project has usually a specified goal and a time limit.
It is often carried out by a team of people who report back to someone else.
A program usually has a set of goals and objectives.
It is usually implemented by a single person.
Statistics
- Hire the top business lawyers and save up to 60% on legal fees (upcounsel.com)
- As of 2020, personal bankers or tellers make an average of $32,620 per year, according to the BLS. (wgu.edu)
- UpCounsel accepts only the top 5 percent of lawyers on its site. (upcounsel.com)
- The profession is expected to grow 7% by 2028, a bit faster than the national average. (wgu.edu)
- Our program is 100% engineered for your success. (online.uc.edu)
External Links
How To
How is Lean Manufacturing done?
Lean Manufacturing is a method to reduce waste and increase efficiency using structured methods. They were developed by Toyota Motor Corporation in Japan during the 1980s. The primary goal was to make products with lower costs and maintain high quality. Lean manufacturing is about eliminating redundant steps and activities from the manufacturing process. It is made up of five elements: continuous improvement, continuous improvement, just in-time, continuous change, and 5S. The production of only what the customer needs without extra work is called pull systems. Continuous improvement involves constantly improving upon existing processes. Just-in-time refers to when components and materials are delivered directly to the point where they are needed. Kaizen is continuous improvement. This can be achieved by making small, incremental changes every day. Five-S stands for sort. It is also the acronym for shine, standardize (standardize), and sustain. These five elements can be combined to achieve the best possible results.
The Lean Production System
Six key concepts are the basis of lean production:
-
Flow - focuses on moving information and materials as close to customers as possible.
-
Value stream mapping- This allows you to break down each step of a process and create a flowchart detailing the entire process.
-
Five S's: Sort, Shine Standardize, Sustain, Set In Order, Shine and Shine
-
Kanban - visual cues such as stickers or colored tape can be used to track inventory.
-
Theory of constraints - identify bottlenecks in the process and eliminate them using lean tools like kanban boards;
-
Just-in time - Get components and materials delivered right at the point of usage;
-
Continuous improvement - make incremental improvements to the process rather than overhauling it all at once.