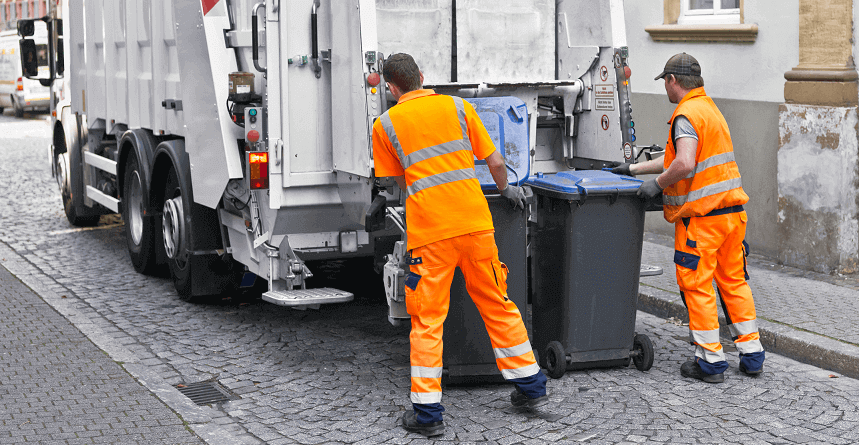
Defining the role of middle management
Middle management is responsible for connecting top-level managers with employees at lower levels. They transform the strategy from the executive team into goals for their department. They collect data, analyze it and then report the results back to the executive team. These responsibilities include overseeing the work of subordinates and making decisions regarding the allocation of resource.
Federal government middle managers are in similar or higher supervisory positions to front-line supervisors. This includes establishing guidelines and policies to govern the work done by lower-level employees.
Mid-managers face many challenges
The conflicting roles of middle managers can lead to frustration. They have to manage their subordinates and report back to higher-ups. But they also have the responsibility of enforcing policies which aren't their own. Their direct reports might not like these policies. Technology can help middle managers deal with this dilemma. PwC's app for middle managers directs them to more than 300 courses and identifies potential digital training opportunities.
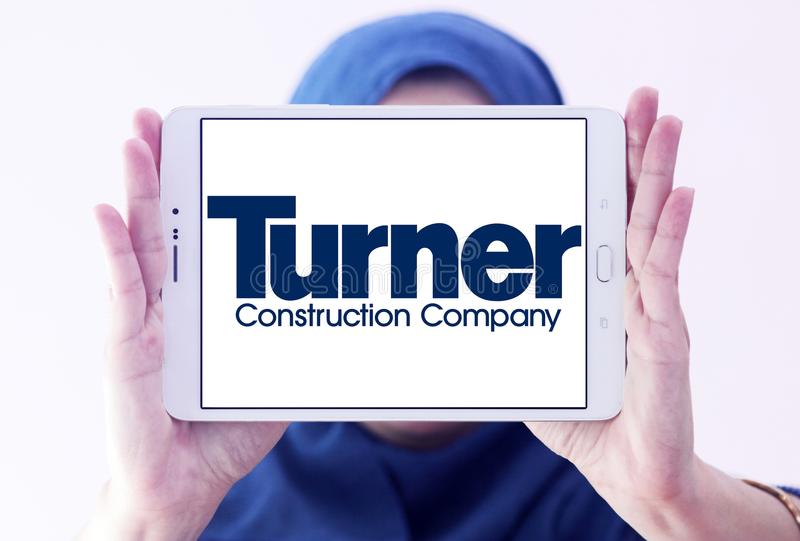
The middle managers need to be able understand all parties and establish a relationship of trust between them. This can be hard because they are often limited in time due to multiple stakeholders. They must prioritize their tasks to ensure that they meet all requirements.
Tools for middle managers to collaborate
Organizations have a crucial role for middle managers. They are responsible for keeping track of project progress and moving information between teams. Communicating with remote workers can be more difficult. There are many tools out there that will help middle managers collaborate better.
Middle managers often have to handle a lot of meetings, which consumes up to 35% of their time. As a result, they have little time to do other work. In addition, they have a high cognitive load due to video communication. This can lead to burnout.
Communication skills
Effective communication skills are vital to the success of middle managers. These professionals work in a demanding job. They must collaborate closely with both the frontline staff and the senior management. Additionally, they have to deal with constant miscommunications and misunderstandings. Their communication skills will help them build trust with others and improve their influence and engagement.
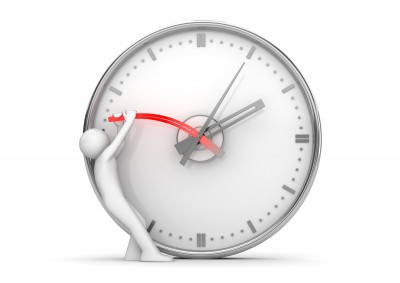
Communication skills in middle management can be crucial in any industry. Middle managers are able to interact with employees directly, unlike senior administrators. This means that they must be able to communicate effectively verbally and in writing. To avoid miscommunication and avoid mistakes, middle managers must be able to communicate clearly and effectively in writing.
FAQ
What are the main four functions of management
Management is responsible in planning, organizing and directing people and resources. It includes the development of policies and procedures as well as setting goals.
Organizations can achieve their goals through management. This includes leadership, coordination, control and motivation.
Management has four primary functions:
Planning - Planning involves determining what needs to be done.
Organizing - Organizing involves deciding how things should be done.
Direction - This is the art of getting people to follow your instructions.
Controlling – Controlling is the process of ensuring that tasks are completed according to plan.
How do you manage employees effectively?
The key to effective management of employees is ensuring their happiness and productivity.
It is important to set clear expectations about their behavior and keep track of their performance.
Managers must set clear goals for their employees and themselves to achieve this goal.
They need to communicate clearly with staff members. They must communicate clearly with staff members.
They also need to keep records of their team's activities. These include:
-
What was achieved?
-
How much work was put in?
-
Who did it, anyway?
-
What was the moment it was completed?
-
Why?
This data can be used to evaluate and monitor performance.
What is TQM?
The industrial revolution led to the birth and growth of the quality movement. Manufacturing companies realized they couldn't compete solely on price. They had to improve efficiency and quality if they were to remain competitive.
In response to this need for improvement, management developed Total Quality Management (TQM), which focused on improving all aspects of an organization's performance. It included continuous improvement, employee involvement and customer satisfaction.
What kind people use Six Sigma?
Six-sigma will be well-known to anyone who has worked in operations research or statistics. However, anyone involved in any aspect of business can benefit from using it.
This requires a lot of dedication, so only people with great leadership skills can make the effort to implement it.
What are management concepts, you ask?
Management concepts are the principles and practices used by managers to manage people, resources. These include topics such as human resource policies and job descriptions, performance assessments, training programs and employee motivation.
Statistics
- UpCounsel accepts only the top 5 percent of lawyers on its site. (upcounsel.com)
- 100% of the courses are offered online, and no campus visits are required — a big time-saver for you. (online.uc.edu)
- The BLS says that financial services jobs like banking are expected to grow 4% by 2030, about as fast as the national average. (wgu.edu)
- The average salary for financial advisors in 2021 is around $60,000 per year, with the top 10% of the profession making more than $111,000 per year. (wgu.edu)
- Our program is 100% engineered for your success. (online.uc.edu)
External Links
How To
How do I do the Kaizen Method?
Kaizen means continuous improvement. This Japanese term refers to the Japanese philosophy of continuous improvement that emphasizes incremental improvements and constant improvement. It is a process where people come together to improve their processes.
Kaizen is one of Lean Manufacturing's most efficient methods. Employees responsible for the production line should identify potential problems in the manufacturing process and work together to resolve them. This way, the quality of products increases, and the cost decreases.
Kaizen is the idea that every worker should be aware of what is going on around them. To prevent problems from happening, any problem should be addressed immediately. If someone is aware of a problem at work, he/she should inform his/her manager immediately.
There are some basic principles that we follow when doing kaizen. The end product is always our starting point and we work toward the beginning. To improve our factory, for example, we need to fix the machines that produce the final product. We then fix the machines producing components, and the machines producing raw materials. Finally, we repair the workers who are directly involved with these machines.
This is why it's called "kaizen" because it works step-by-step to improve everything. Once we have finished fixing the factory, we return to the beginning and work until perfection.
It is important to understand how to measure the effectiveness and implementation of kaizen in your company. There are several ways that you can tell if your kaizen system is working. One method is to inspect the finished products for defects. Another method is to determine how much productivity has improved since the implementation of kaizen.
A good way to determine whether kaizen has been implemented is to ask why. You were trying to save money or obey the law? You really believed it would make you successful?
If you answered yes to any one of these questions, congratulations! You are now ready to begin kaizen.