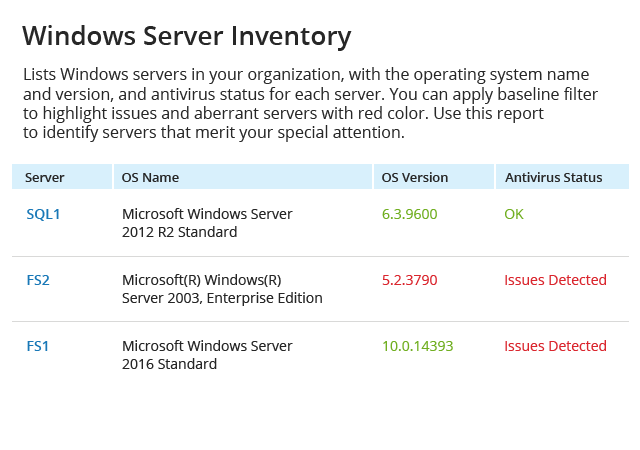
For more than a full year, the Department of Homeland Security ("DHS") has been publicly focusing on the supply chain risk. As a result, agencies and contractors are now expected to take more active roles in protecting the nation's supply chains. This is an important issue that needs more attention than ever, regardless of industry. Contractors and agencies must now comply with DHS’s supply chain standards. They are continuously being updated.
SVIP
The Phase 1 Awards have been announced by the Department of Homeland Security for the Silicon Valley Innovation Program (SVIP). The principal goal of the program is to make distributed ledger technology more effective in preventing forgeries and fakes of licenses, certificates, and other documents. The government is looking to start-ups with innovative solutions for the problem of counterfeits and prevention. To help achieve its goals, SVIP partnered with several start-ups in order to create blockchain-based solutions.
ESOC
ESOC DHS Supply is a team of analysts responsible for providing cross-organizational threat intelligence program compliance and maintenance to the Department of Defense. Commerce Threat Intelligence Portal is also maintained by the organization. This portal collects and distributes information about cyber security. ESOC utilizes enterprise event correlation (EEC) to apply correlation logic to ingested security logs. ArcSight logs an average of more than three billion events each week. This number will rise as more data feeds are added.
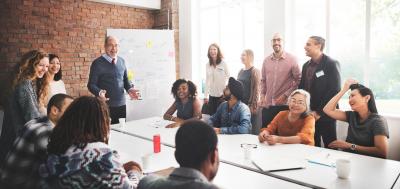
CBTS
Texas A&M University System (DHS) have created a Center of Excellence to Screen Cross-Border Threats and Protect Supply Chains. This center will be developing new tools and techniques to help detect and prevent biological threats. The Center's mission is to build a workforce capable of dealing with any biological threats. With this grant, Texas A&M University will lead a consortium of universities to develop solutions that will protect the U.S. food supply chain.
GSA
GSA schedules and DHS supply lists are great for buying goods for your organization. They can be negotiated through GSA, and are accessible to local and state governments. These government agencies and their employees can also be sold through the GSA schedules. Visit the GSA website to get started. This page will show you the types of products and services available through these schedules. The schedules will allow you to buy any product or service you need and give you a significant discount.
DoC
The DoC for DHHS is the federal government's lead agency for procuring essential health and human services supplies. It is the country's biggest procuring agency, and leverages its purchasing power in order to obtain the best prices. The new procurement strategy of DHHS will be fully implemented by 2018. The Department is committed to developing new technologies to improve the manufacturing of key medications and products. It partners with industry to increase domestic production capacity for these important products.
NRMC
The NRMC has a new chair. Mara Winn will replace Bob Kolasky as the co-chair of the Supply Chain Risk Management Task Force. In the taskforce, she will represent the U.S. government. She will share the chairmanship with an executive from the U.S. telecommunications industry. She is also an employee of the Information Technology Industry Council. She has been a part of the Transportation Security Administration as well as the Innovation Task Force during her time at the Department of Homeland Security.
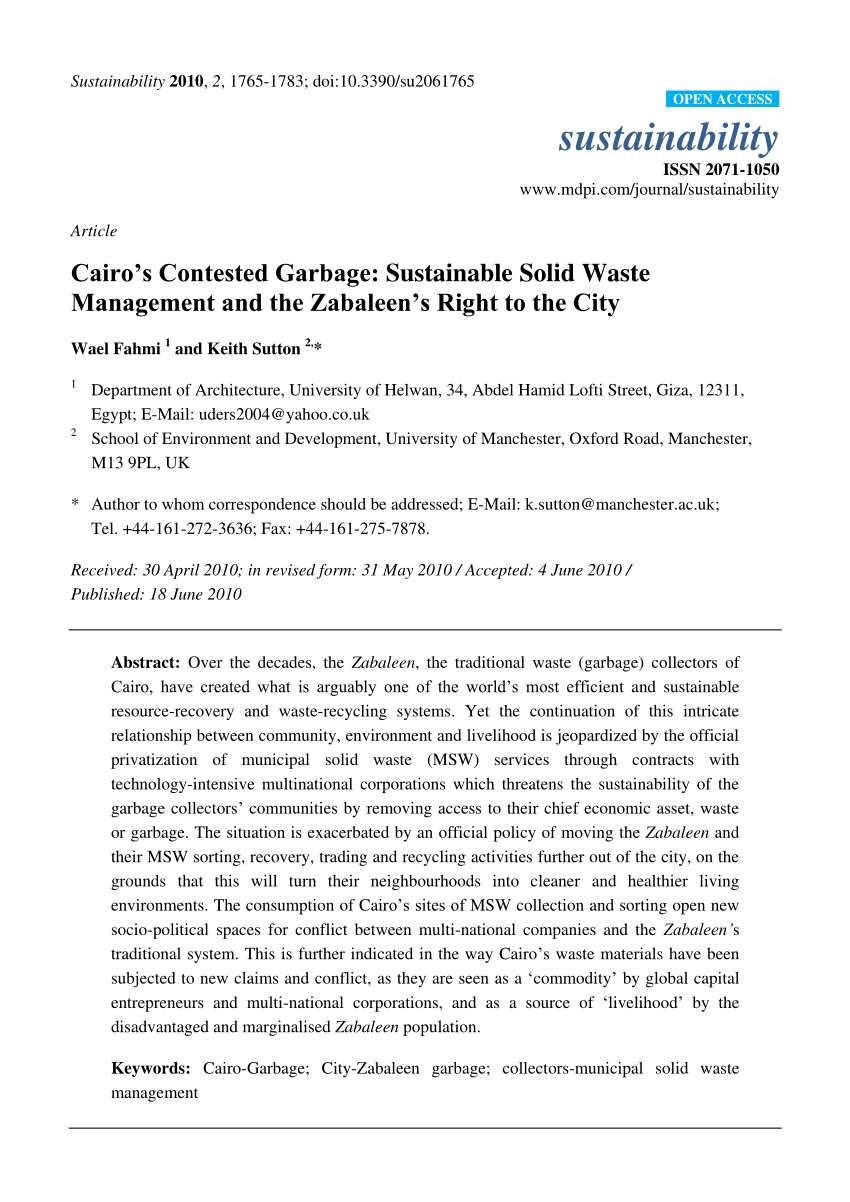
CMMC
CMMC to DHS supply chain security is a big step forward considering the special jurisdiction of DHS over national Infrastructure. This could increase the security of DHS' supply chain. While CMMC is an already-used technology in DoD contracts it could take some time for the DoD to officially adopt the program. This article was originally published by Homeland Security Today.
OTAs
DHS supply OTAs can be negotiated with commercial firms. In March 2017, the Department of Homeland Security tried to initiate the first OTA project. The project was valued in excess of $125 millions. The project was to provide funding for prototype development at the Border Security Technology Consortium. DHS ruled that the proposals weren’t original or offered innovative solutions. As of April 2018, no OTA projects had been completed and two more were under review.
CyberRx
The Department of Homeland Security is launching a new initiative to prepare the healthcare sector for cybersecurity threats. CyberRX is an industry wide initiative to help organizations better prepare for cybersecurity threats. The exercises cover three key areas: information systems; medical devices; and essential technology resource. Participants receive guidance and cybersecurity training. CyberRX provides guidance and cybersecurity training to help organizations understand the potential risks of a cyberattack.
FAQ
What is Six Sigma, exactly?
It's a method for quality improvement that focuses on customer service as well as continuous learning. The goal is to eliminate defects by using statistical techniques.
Motorola's 1986 efforts to improve manufacturing process efficiency led to the creation of Six Sigma.
It was quickly adopted by the industry and many companies are now using six-sigma to improve product design, production, delivery, customer service, and product design.
What is the meaning of "project management?"
That is the management of all activities associated with a project.
We help you define the scope of your project, identify the requirements, prepare the budget, organize the team, plan the work, monitor progress and evaluate the results before closing down the project.
What are the top management skills?
Managerial skills are crucial for every business owner, regardless of whether they run a small store in their locality or a large corporation. They include the ability to manage people, finances, resources, time, and space, as well as other factors.
These skills are necessary for setting goals and objectives as well as planning strategies, leading groups, motivating employees and solving problems.
As you can see, there are many managerial responsibilities!
What is TQM?
The quality movement was born during the industrial revolution when manufacturing companies realized they could not compete on price alone. They needed to improve quality and efficiency if they were going to remain competitive.
Management responded to the need to improve, and developed Total Quality Management (TQM). This focused on improving every aspect of an organization’s performance. It included continuous improvement processes, employee involvement, and customer satisfaction.
What is the difference between TQM and Six Sigma?
The main difference between these two quality-management tools is that six-sigma concentrates on eliminating defects while total QM (TQM), focuses upon improving processes and reducing expenses.
Six Sigma is a methodology for continuous improvement. This method emphasizes eliminating defects using statistical methods such p-charts, control charts, and Pareto analysis.
The goal of this method is to reduce variation in product output. This is achieved by identifying and addressing the root causes of problems.
Total quality management refers to the monitoring and measurement of all aspects in an organization. It also includes the training of employees to improve performance.
It is frequently used as an approach to increasing productivity.
What are the most common errors made by managers?
Managers sometimes make their own job harder than necessary.
They may not be able to delegate enough responsibility to staff or provide adequate support.
A majority of managers lack the communication skills needed to motivate their team and lead them.
Managers can set unrealistic expectations for their employees.
Managers may attempt to solve all problems themselves, rather than delegating it to others.
What are the five management steps?
The five stages of a business include planning, execution (monitoring), review, evaluation, and review.
Setting goals for the future requires planning. It includes defining what you want to achieve and how you plan to do it.
Execution happens when you actually do the plan. You need to make sure they're followed by everyone involved.
Monitoring is the act of monitoring your progress towards achieving your targets. This should involve regular reviews of performance against targets and budgets.
At the end of every year, reviews take place. They are a chance to see if everything went smoothly during the year. If not then, you can make changes to improve your performance next year.
Evaluation takes place after the annual review. It helps identify what worked well and what didn't. It provides feedback about how people perform.
Statistics
- 100% of the courses are offered online, and no campus visits are required — a big time-saver for you. (online.uc.edu)
- The profession is expected to grow 7% by 2028, a bit faster than the national average. (wgu.edu)
- Your choice in Step 5 may very likely be the same or similar to the alternative you placed at the top of your list at the end of Step 4. (umassd.edu)
- The BLS says that financial services jobs like banking are expected to grow 4% by 2030, about as fast as the national average. (wgu.edu)
- The average salary for financial advisors in 2021 is around $60,000 per year, with the top 10% of the profession making more than $111,000 per year. (wgu.edu)
External Links
How To
How do you implement Quality Management Plans (QMPs)?
Quality Management Plan (QMP), which was introduced in ISO 9001:2008, provides a systematic approach to improving processes, products, and services through continual improvement. It provides a systematic approach to improving processes, products and customer satisfaction by continuously measuring, analysing, controlling, controlling, and improving them.
QMP is a common method to ensure business performance. The QMP aims to improve the process of production, service delivery, and customer relationship. QMPs must include all three elements - Products, Services, and Processes. If the QMP focuses on one aspect, it is called "Process." QMP. The QMP that focuses on a Product/Service is called a "Product." QMP. QMP stands for Customer Relationships.
When implementing a QMP, there are two main elements: Scope and Strategy. They can be described as follows:
Scope is what the QMP covers and how long it will last. This scope can be used to determine activities for the first six-months of implementation of a QMP in your company.
Strategy: This describes how you will achieve the goals in your scope.
A typical QMP comprises five phases: Planning and Design, Development, Construction, Implementation, Maintenance. Each phase is described below:
Planning: In this stage, the objectives of the QMP are identified and prioritized. All stakeholders involved in the project are consulted to understand their requirements and expectations. After identifying the objectives, priorities, and stakeholder involvement, the next step is to develop the strategy for achieving these objectives.
Design: During this stage, the design team develops the vision, mission, strategies, and tactics required for the successful implementation of the QMP. These strategies are executed by creating detailed plans.
Development: Here the development team works toward building the necessary resources and capabilities to support the successful implementation.
Implementation: This involves the actual implementation of the QMP using the planned strategies.
Maintenance: It is an ongoing process that maintains the QMP over time.
In addition, several additional items must be included in the QMP:
Stakeholder involvement is important for the QMP's success. They should be involved in planning, design, development and implementation of the QMP.
Project Initiation: It is essential to have a clear understanding about the problem and the solution before you can initiate a project. The initiator must know the reason they are doing something and the expected outcome.
Time Frame: The time frame of the QMP is very critical. If you plan to implement the QMP for a short period, you can start with a simple version. For a long-term commitment you may need more complicated versions.
Cost Estimation - Cost estimation is an important part of the QMP. Planning is not possible without knowing the amount of money you will spend. Cost estimation is crucial before you begin the QMP.
QMPs are not just a written document. They should be a living document. It evolves as the company grows and changes. So, it should be reviewed periodically to make sure that it still meets the needs of the organization.